前回まで一通りコメットの開発における問題点を考えてきた。
特に前回は、開発の総仕上げとなる試験飛行について考えた。
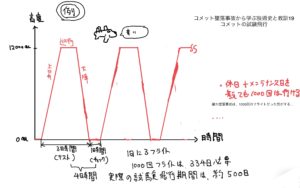
今回は、コメットの事故への対応の様子を考えていこう。
まずは、復習になってしまうが基本的な事故対応の流れをもう一度、簡単に紹介しよう。
事故対応の基本的な考え方と進め方
事故対応の一般的な考え方と流れは以前に説明した。
事故対応の考え方の詳細→コメット墜落事故から学ぶ技術史と教訓9 コメット墜落事故と原因探し(破壊工学、FTA、FMEA、特性要因図、仮説と実証)
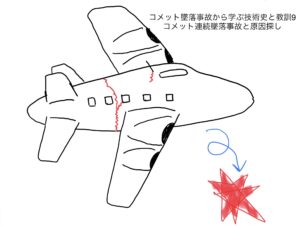
事故を起こした機械の部品を集めるて分析する
少し復習になるが機械の不具合、事故の対応への第一歩は、事象品の回収だ。
どんなに細かい部品でもなるべく多くの部品、欠片を総力を結集してかき集める。
次にかき集めた部品、欠片を元の形に戻るようにパズルのように復元していく。
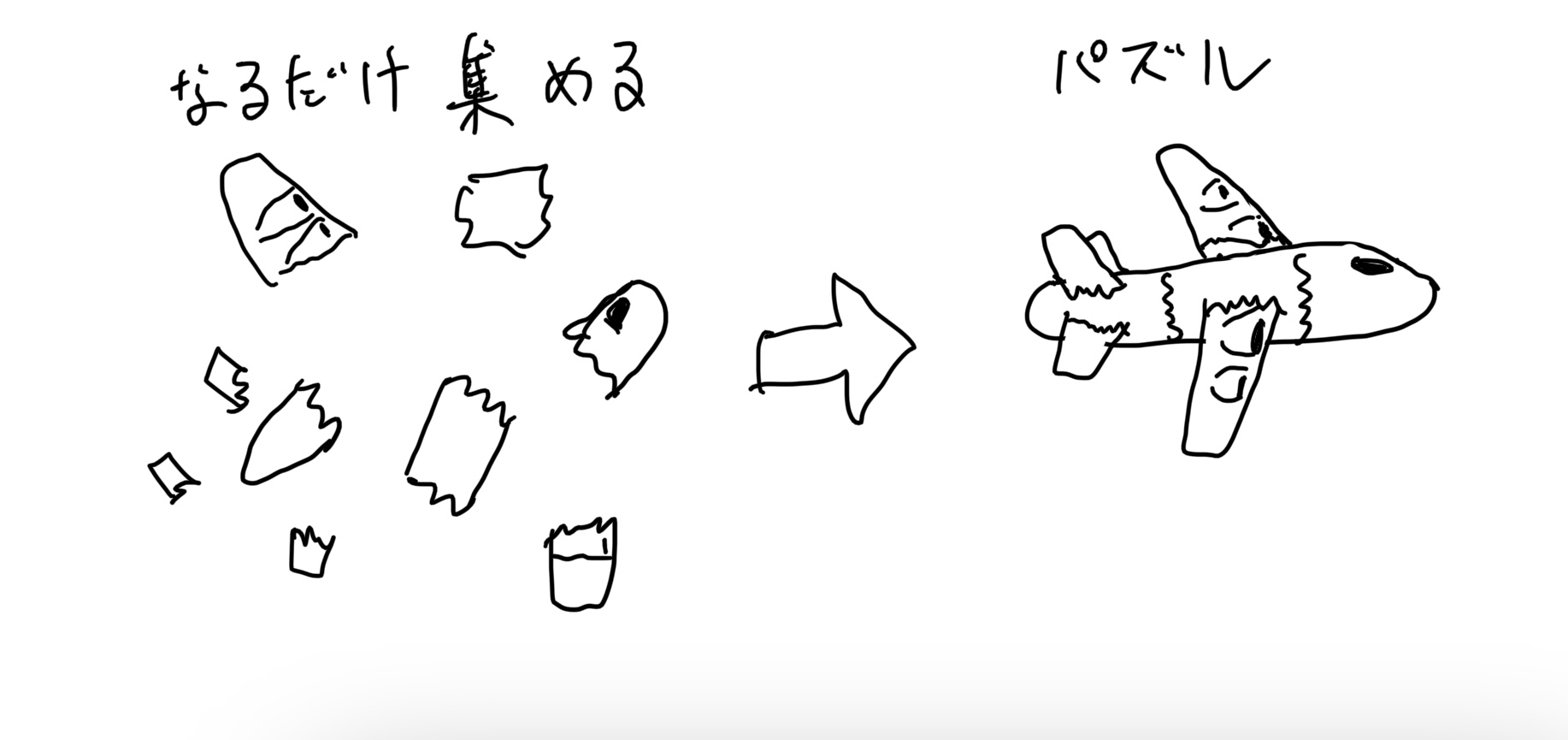
集めた部品、欠片を元の形に戻せたら、次に破損した部品の破断面を全てチェックする。
その破断面に残っている形跡は、一発破壊なのか疲労破壊なのか、もしくは疲労破壊と一発破壊の組み合わせなのかを仕分ける。
破壊の形態さえわかれば、ある程度の経験のあるエンジニアならば破壊が発生した順番がわかる。
ここまでの作業で機械のどの部品が最初に破壊したか、部品のどの部位が最初に破壊したのかがわかる。
ここから先は、多くの人を集めて原因の仮説を考えるのだ。
事故の発生原因の仮説作り
この事故原因の仮説作りを軽くおさらいするとFTA、FMEA、特性要因図などを使って分析する。
基本的にFTAは部品の破壊をトップ事象において考え、どのような事象が発生すれば部品の破損が発生するのか少しづつ細くしていく分析方法だ。
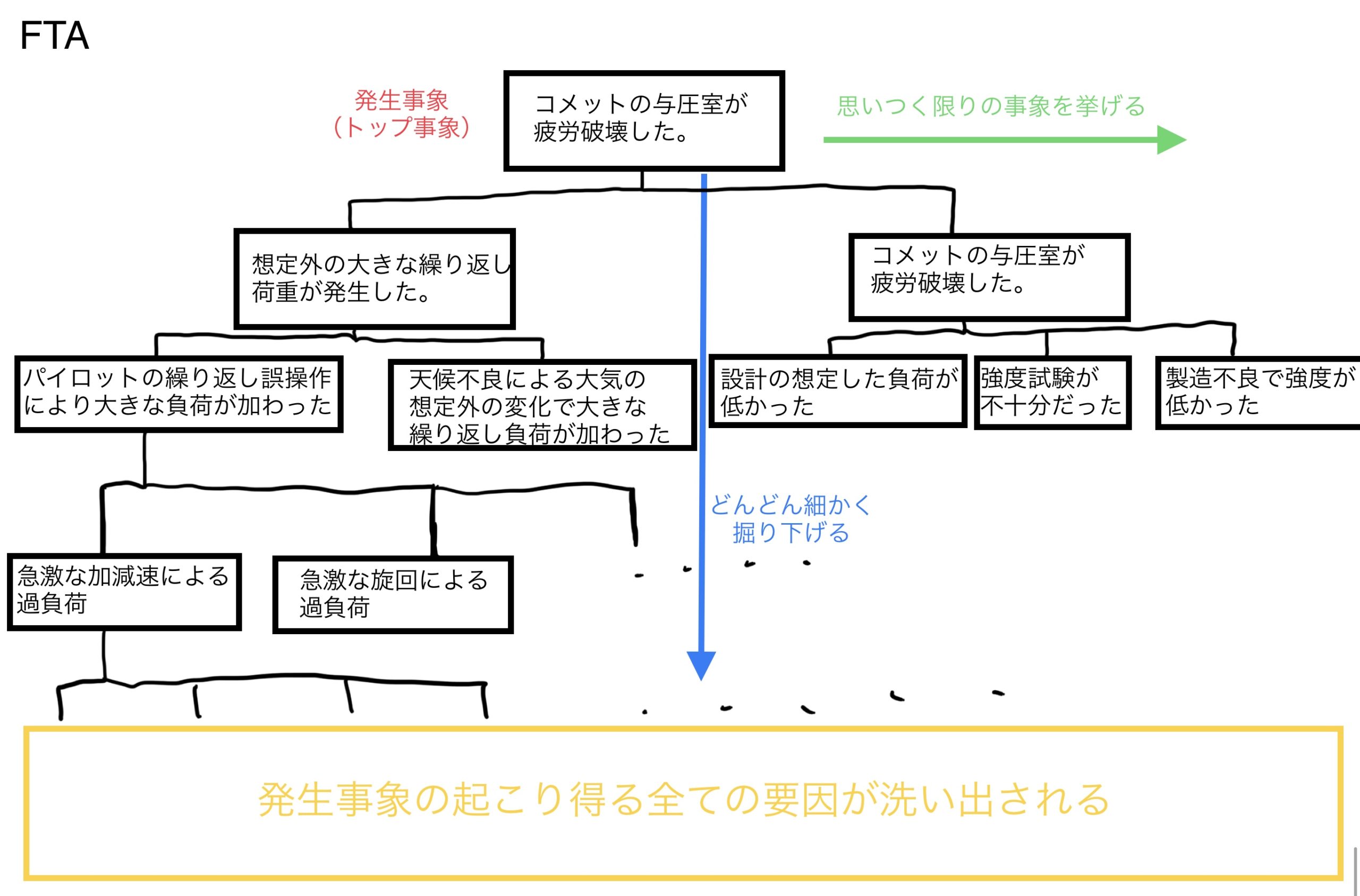
一方でFMEAは、FTAと逆にまず全ての部品から起こり得る破壊形態を考えて、その部品が破壊すると機械全体にどのような影響を及ぼすのかを考える方法だ。
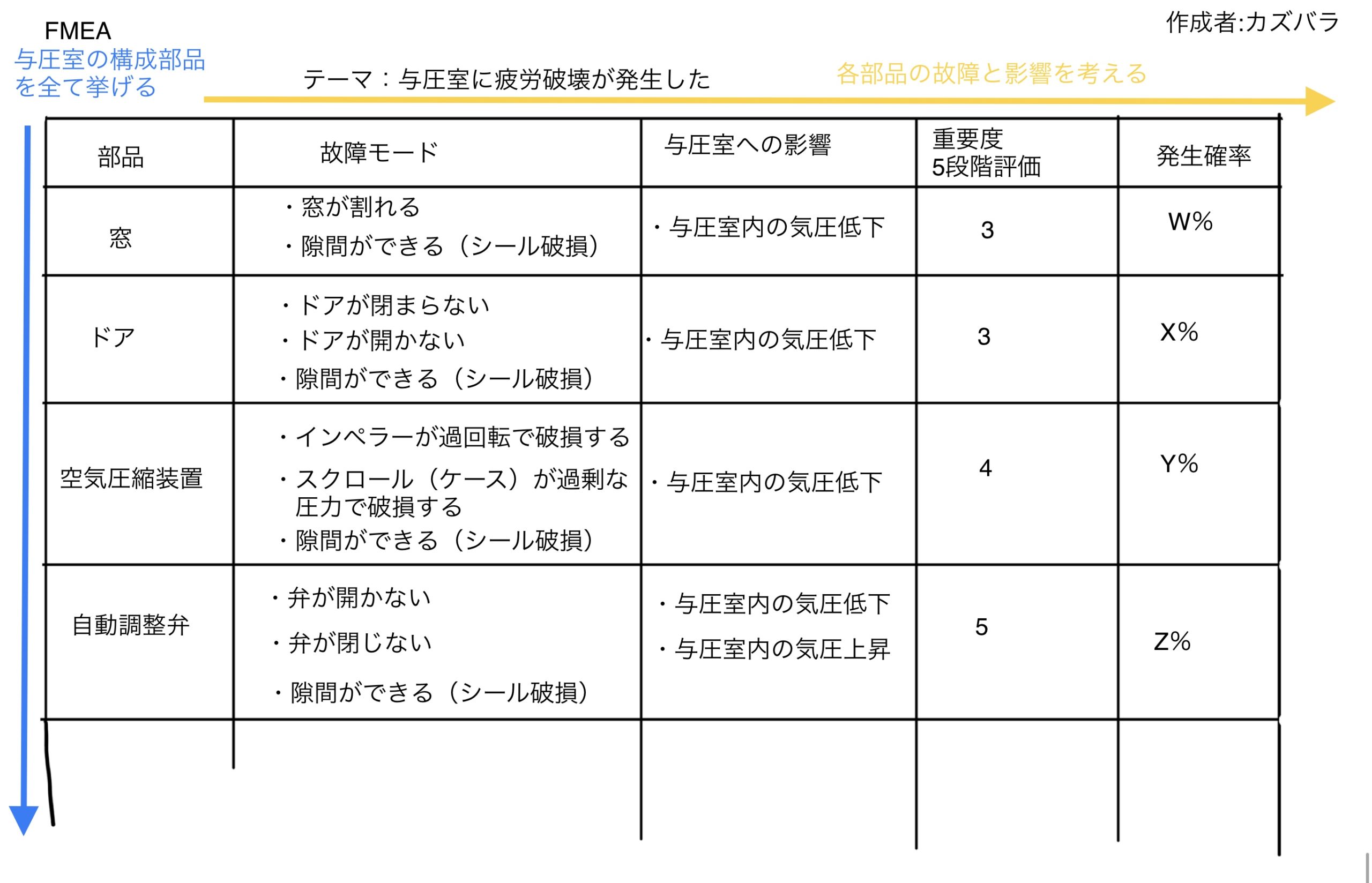
つまりFTAとFMEAはアプローチが全くの逆で、FTAはトップ事象から様々な事象を考えて、どんどん問題点を細かく分解していく方法でFMEAは、最初に機械の一番細かい構成部品から破壊を考えて行って最終的に機械全体にどのような影響が出るのかを考えていくやり方だ。
常にどちらも実施する時間があるのがベストだが事故の内容や機械の種類によって使い分けても良い。
最後に特性要因図だが、この分析方法は機械に関係する周囲に問題がないか探る方法だ。
代表的な要素だと5Mと呼ばれていて機械(Machine)、人(Man)、製造(Manufacture ) 、運用(Method),計測(Measure)の軸で考えると良い。
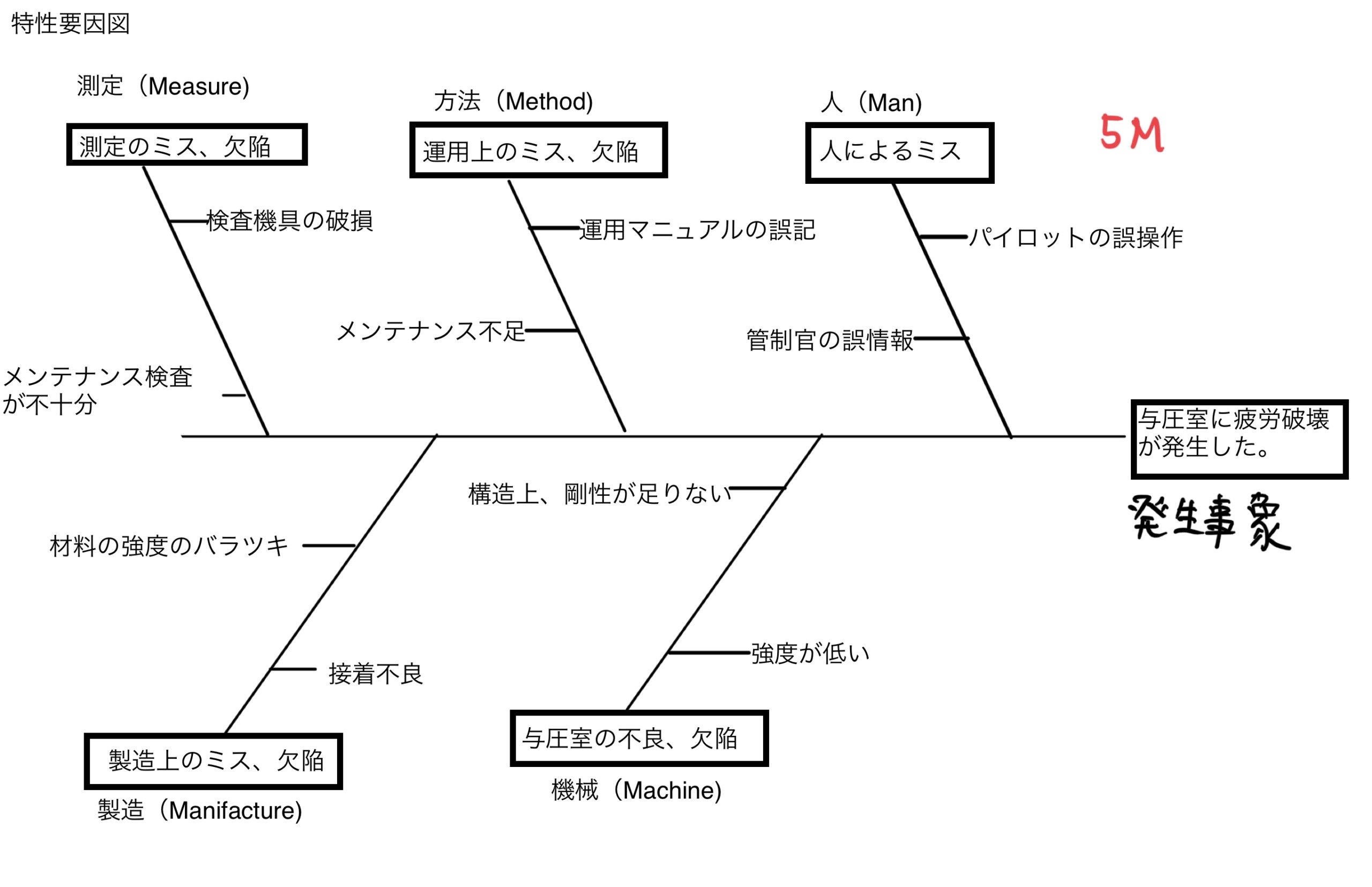
これはあくまで5Mは、推奨する要素なだけでもし輸送、部品保管など他にも関連する要素があればどんどん付け足した方が良い分析になる。
このような主に3つの分析をメインに最も可能性の高い仮説を作成する。
後は、仮説には、必ず必要になる実証を示さなければならないので実証実験を行う。
再現テスト
実証実験の作成の考え方は、こちらで紹介した。
再現テストの作成の考え方→コメット墜落事故から学ぶ技術史と教訓10 コメット墜落事故の再現テストと原因解明(再現テスト、ひずみゲージ、ロードセル、信頼性工学)

基本的には仮説で考えた状況をそのままなんらかの方法で再現することを考えてから信頼性工学を使って実際に再現できているかを確認し再現テストを作成する。
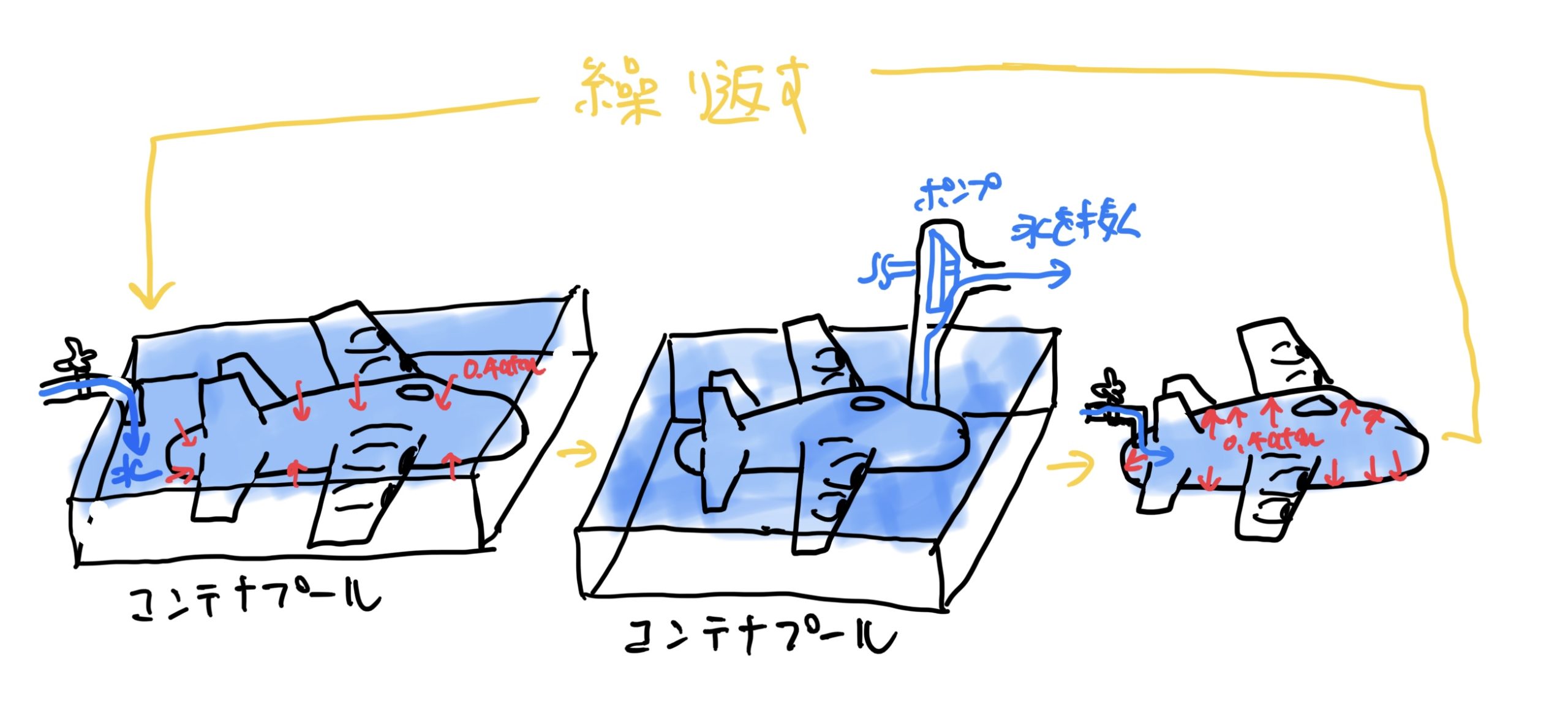
後は、再現テストが終わって仮説が無事に立証できれば仮説が真実に近づくのだ。
事故対応の考え方、方法のまとめ
ここまでの事故対応の流れをフローチャート風に書くと次のようになる。
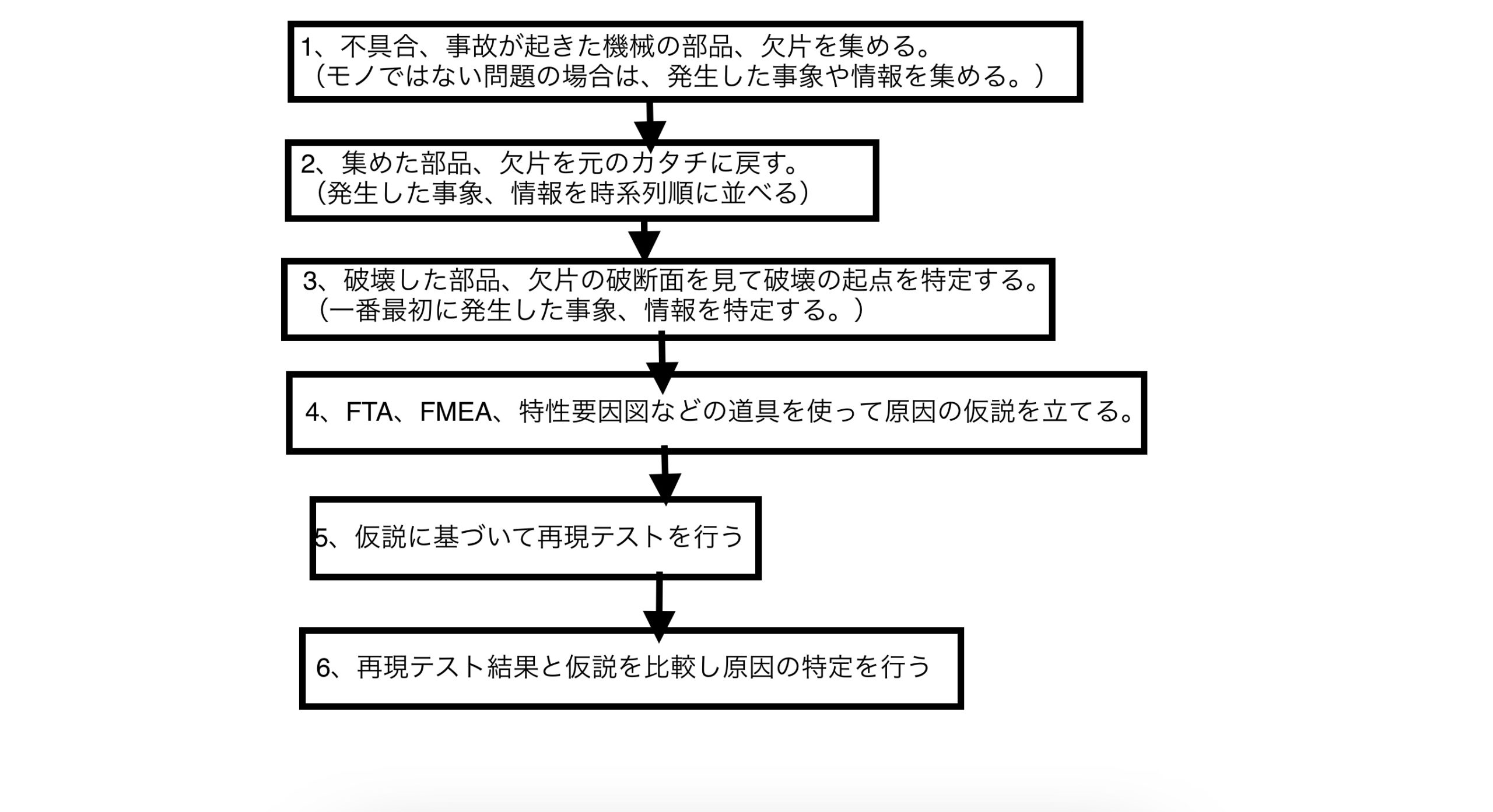
基本的に内容を全て覚えている必要はないが、このフローチャートを覚えておくと事故対応だけでなく日々の生活での不具合、トラブルから日常の仕事で多発する問題の解決の考え方として非常に有用なのでもし気が向いたら紙にでも書いてやってもらえると筆者は、嬉しい。
ただ普段使いするポイントは、あまり考えすぎないことだ。
一つの分析に手こずって次に進めないようであれば飛ばして先に進めたほうが良い。
また、もし家族や職場の仲間などの協力が期待できる場合は、どんどん手伝ってもらうと分析の精度が良くなりより速く進む。
以上、ここまでがおさらいになる。
ここからコメットの事故対応を見ていこう。
コメット連続墜落事故の対応
コメットの事故の時系列の出来事や対応、再現テスト、原因解明までの動きは以前に紹介したので割愛する。
墜落事故の時系列と原因探し→コメット墜落事故から学ぶ技術史と教訓9 コメット墜落事故と原因探し(破壊工学、FTA、FMEA、特性要因図、仮説と実証)
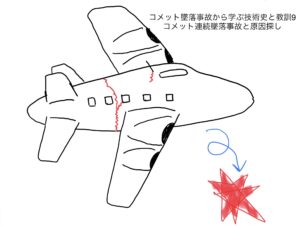
RAEによる再現テストと原因解明→コメット墜落事故から学ぶ技術史と教訓10 コメット墜落事故の再現テストと原因解明(再現テスト、ひずみゲージ、ロードセル、信頼性工学)

また筆者なりの事故への考え方、事故対応のための多視点チェック、相互チェックに関してもこちらで紹介した。
事故の考え方と多視点、相互チェック→コメット墜落事故から学ぶ技術史と教訓13 コメット墜落事故の一般的な教訓と原因の再考(応力集中、疲労破壊、多視点チェック、相互チェック)
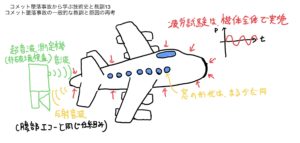
これらを踏まえて今までで説明した工学的なこと、RAEの再現テスト関連以外を中心に考えていこう。
まずは、おさらいになるが事故の時系列をヘビ図で見てみよう。
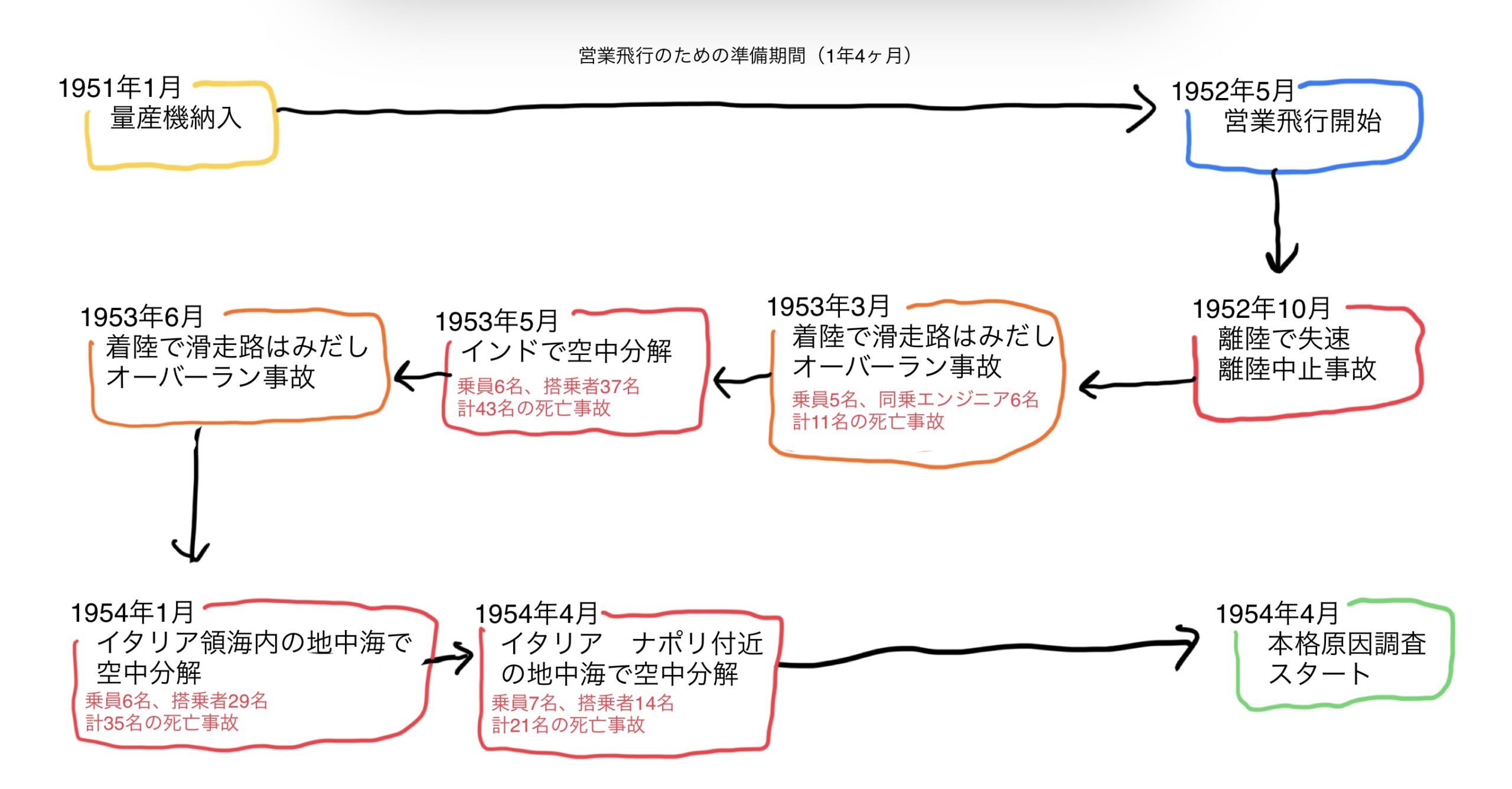
ここで誰もが大きく感じる疑問、問題点が“なぜ、1件目の事故、2件目の事故で本格的に調査に乗り出さなかったのか“だと思う。
1件目の墜落事故対応を考える 1953年 英国航空783便
まず1件目の事故である1953年5月の英国783便の事故対応を見て行こう。
この事故対応は、筆者が今までに見たり聞いたり調べた事故対応の中でも最悪の部類に入る対応だ。
この事故で政府と開発製造会社が導き出した原因の結論は、パイロットの操作ミスである。
さらにインド政府の調査で事故の当日は、天候が悪く雷雲があったとされ、この状況がなおのことパイロットの操作ミスを誘発したと考えた。
あまりにも短絡的な結論である。
しかも地上試験で一発試験を破壊するまで実施してないのでパイロットが操作ミスをしていたとしても、どのくらいの過負荷でどのような壊れ方をするか知っている人は、誰もいない恐ろしい状況なのにあり得ない結論である。
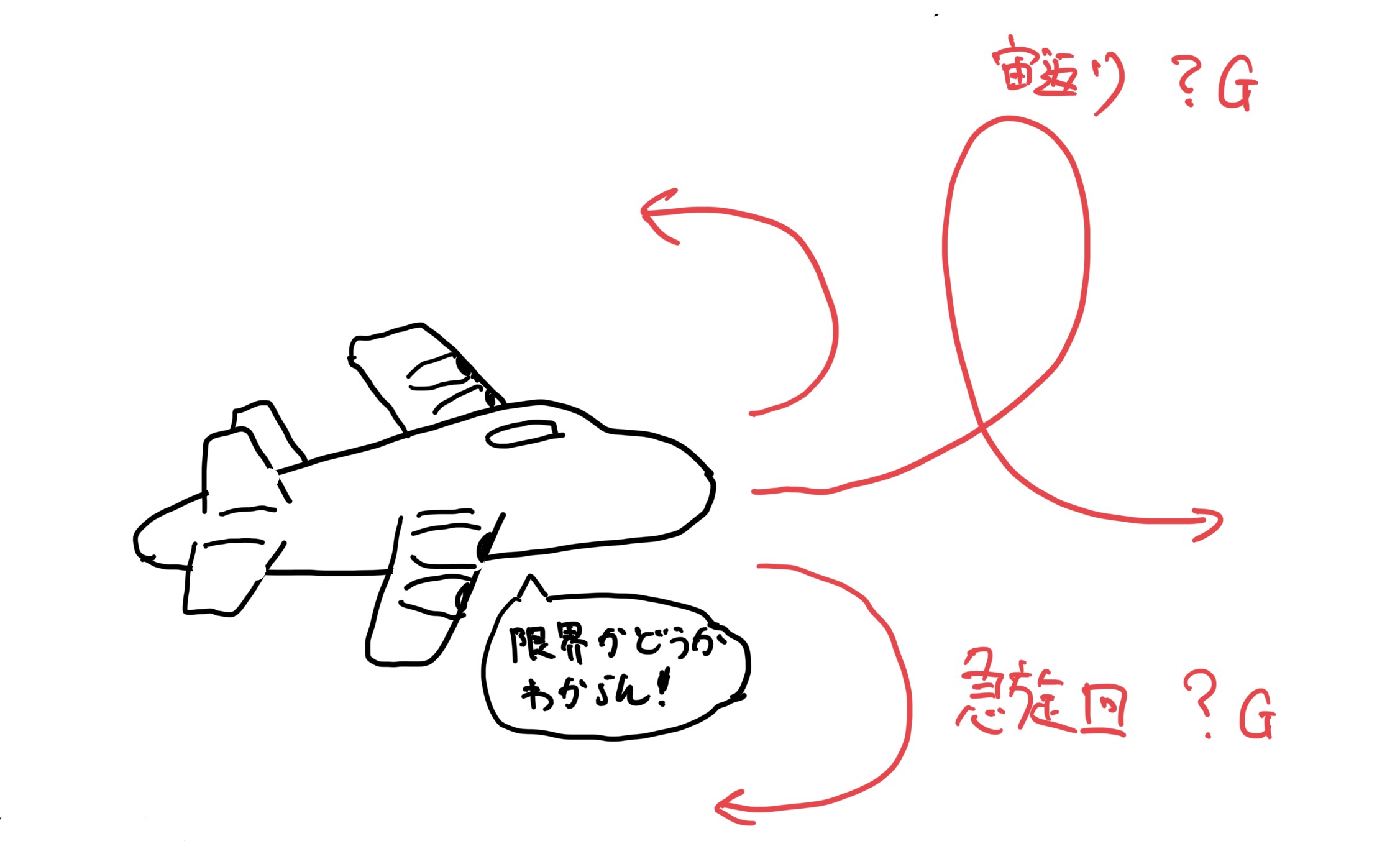
このような原因特定を行わないで導き出されることを憶測や推測などと呼び、ほとんど意味がない。
以前にも述べたが過失割合はどうであれ事故の原因は100%人が悪いということはほとんどなくて、多少でも機械に問題があるものなのだ(特にプロが使う場合)。
さらに普通のエンジニアの考え方では人間はミスをする生き物なので、そのミスを技術や機体でカバーできるように考える。
しかも、この事故について筆者の方で調べてもまともな原因調査を行った形跡はなく、何故かあっさりとパイロットのミスと断定されている。
結局、パイロットのミスとなり大した調査も行わず何の対策もされずに飛行許可は取り消されなかった。
どうも、この段階から与圧室に対する欠陥を指摘する人もいたようだが相手にされていなかったようだ。
筆者の考察だけでも開発だけであれだけのミスや検討違いなどがあったにも関わらず、この段階においても機体の不具合をほとんど疑わなかったようだ。
これは完全に開発製造会社と認可を出した英国政府の自分への驕り、過信を感じる。
大掛かりな事故調査が行われなくてもこのような事故が起きた場合は、普通だったら開発製造会社で開発内容、開発データの見直しくらいはやるものだ。
もし開発製造会社にそのような動きがない場合は、政府が命じて開発内容、開発データの再チェックくらいをやらせることなんか簡単だ。
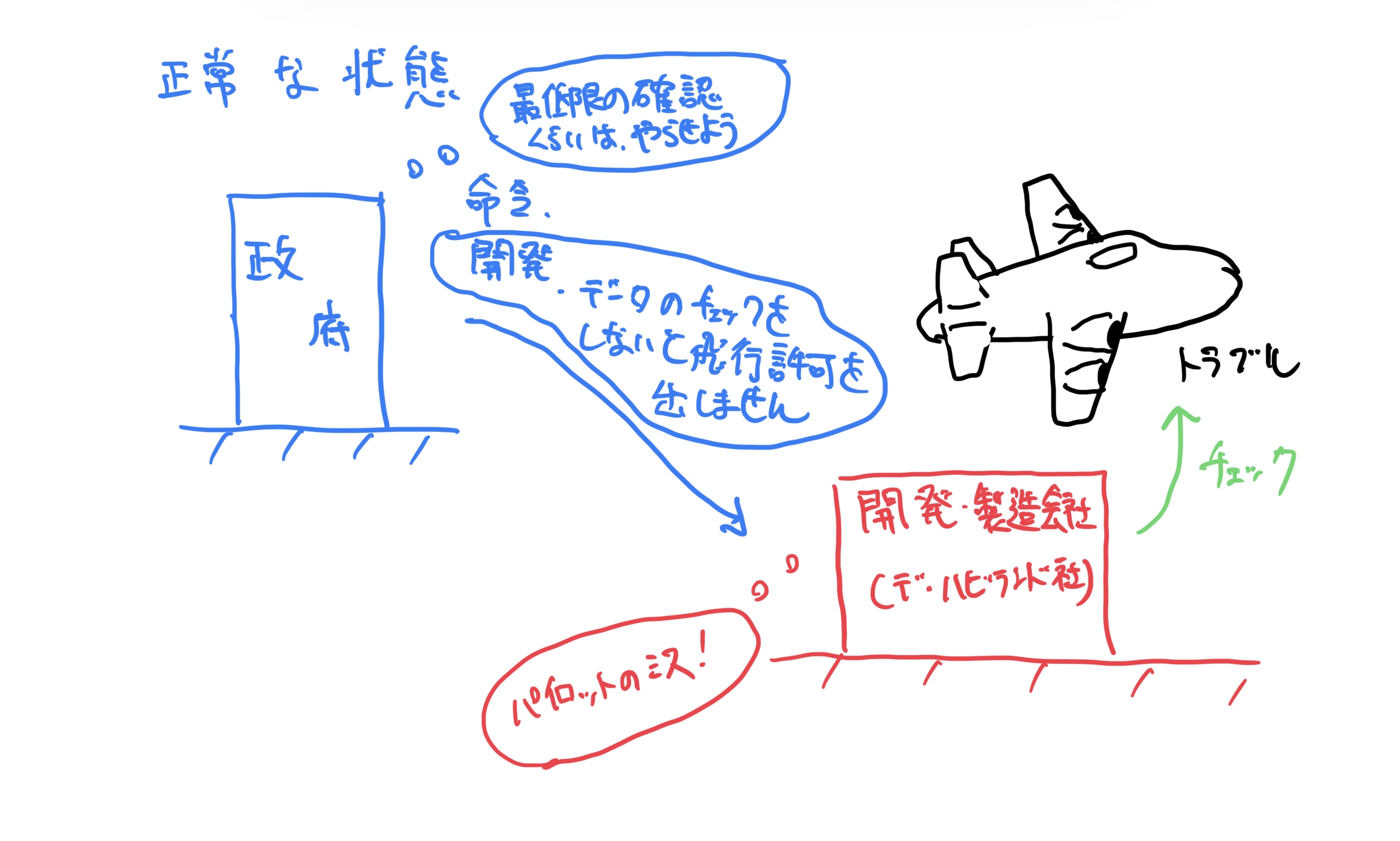
それすら実施した形跡がない。
また通常の事故対応なら、いくらパイロットの操作ミスが原因として濃厚だとしても、断定できない場合は、政府か開発製造会社で事故調査チームを作成して調査するのが普通だ(しかも世界初なので何が起きてもおかしくないので慎重にやる)。
仮にコメットが営業飛行を再開しても念のために水面下で事故の検証は、続けるのが普通だ。
もしここで調査をしっかり行なっていれば歴史は良い方向に変わっていたはずだ。
市場での不具合、事故対応は早急な真の原因探し、原因解明と正しい対策が必ずセットになるのだが、この事故では原因探しどころか対策すらしないひどい有様だ。
どうも政府も開発製造会社の両方ともコメットをとにかく速く営業飛行をさせたいという欲に目が眩んだとしか思えない。
2件目の墜落事故対応を考える 1954年1月 英国航空781便
次の2件目の事故である1954年1月の英国航空781便が空中分解した後に一応の対策らしいことはやったようだ。
内容は、以前にも書いたが当時に流行していた飛行中の機内火災対策(コメットでは発生していない)で火災に関係する燃料系と電気系の防護策を中心に60箇所ほど改修したようだ。
しかし遺体の調査から火災による火傷の後も火事による爆発で生じる金属片も見つかってなかった。
つまり機内火災は、発生していないと証拠から判断できるのだ。
この対策は、全くの無意味で上で説明したような事象の原因解明をしないで、コメットとは別の航空機での飛行中の機内火災が流行っていたので、その対応を取り敢えずコメットにしただけである。
当たり前だが原因が分かってないのに対策をしても全く意味がないのだ。
仮説と検証がセットであるのと同じように不具合、事故対応とは、必ず原因特定と対策案はセットでなければ意味がない。
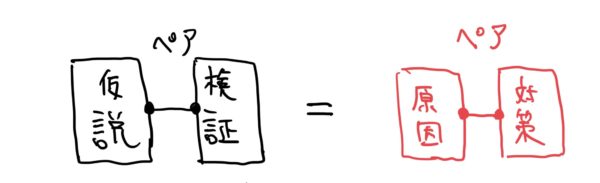
この対応は、単に将来、コメットでも起きるかもしれない機内火災への予防をしただけで対策ではない。
普通の論理で考えれば、いくらなんらかの対応をしても原因がわからない以上、再飛行許可は出ないのだが、何故かイギリス政府の許可が出た。
もうここで1件目の事故に加え、政府の判断が完全に間違えているのである。
おそらくコメットの栄光に傷をつけたくない、飛行できないことによる営業的な損失、政治的な損失と安全を天秤にかけた時に選択をしては、いけない方を選んでしまったのだろう。
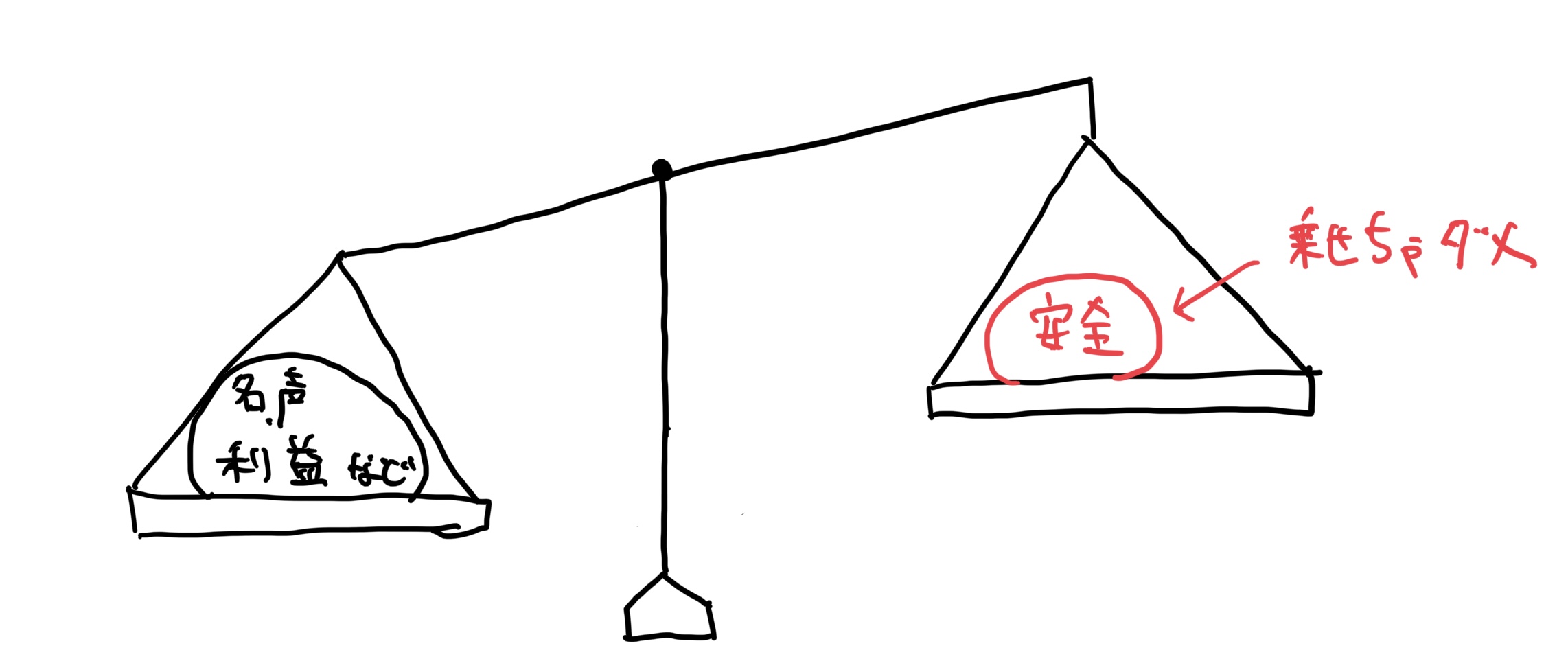
また名門である開発製造会社(デ・ハビランド社)を信じてしまったのであろう。
そもそも安全は、最優先事項で天秤に乗せて何かと比較する対象ではなく、何よりも優先されることなのだ。
この段階でも本来、政府は開発製造会社のチェック機関のはずだが、それが全く機能していなかったことになる。
一方で開発製造会社の動きを見るとこれもあり得ないことである。
通常のまともな会社ならばこのような事態が起きた時点で上で説明したような、この物語で言えばチャーチルによって結集された事故調査チームやRAEのような動きを即座に取るのだ(最近の日本企業もこれができてないことが多い)。
そりゃ国家プロジェクト並みの予算、人員には、できないものの開発製造会社(デ・ハビランド社)は相当な名門、巨大企業だったのでかなりの高い能力、それなりの規模を持った調査チームが組めたはずである。
ここで重要なのが、なんで原因調査をこの段階でやらなかったかと言うと筆者の経験で考えると主な理由が4つほどあって
・さほど大きな社会的な問題だと認識していない
・自分達に大きな責任はない
・お金、時間、人が、かなり奪われて他の事業に差し障る
・儲からない
と思っている節がある。
これは、現代の日本でも不具合対策に対する認識が一緒なのだ。
だから社内の人間も誰もやりたがらないし、評価もつかない、予算も下りない、そもそも会社にやる気がないの4拍子になるのである。
多くの企業で同じだと思うが、企業がこのような心理状態に陥る要因としては社内の開発がどれだけ杜撰だったり開発で多くのトラブルが起きても一度、市場に出したものに対しては、完璧な物を出したと言い張るクセがある。
どうも企業は、他者から責められのがとても嫌なようで一度、市場に出した製品の不具合は、頑なになかなか認めようとしないのだ。
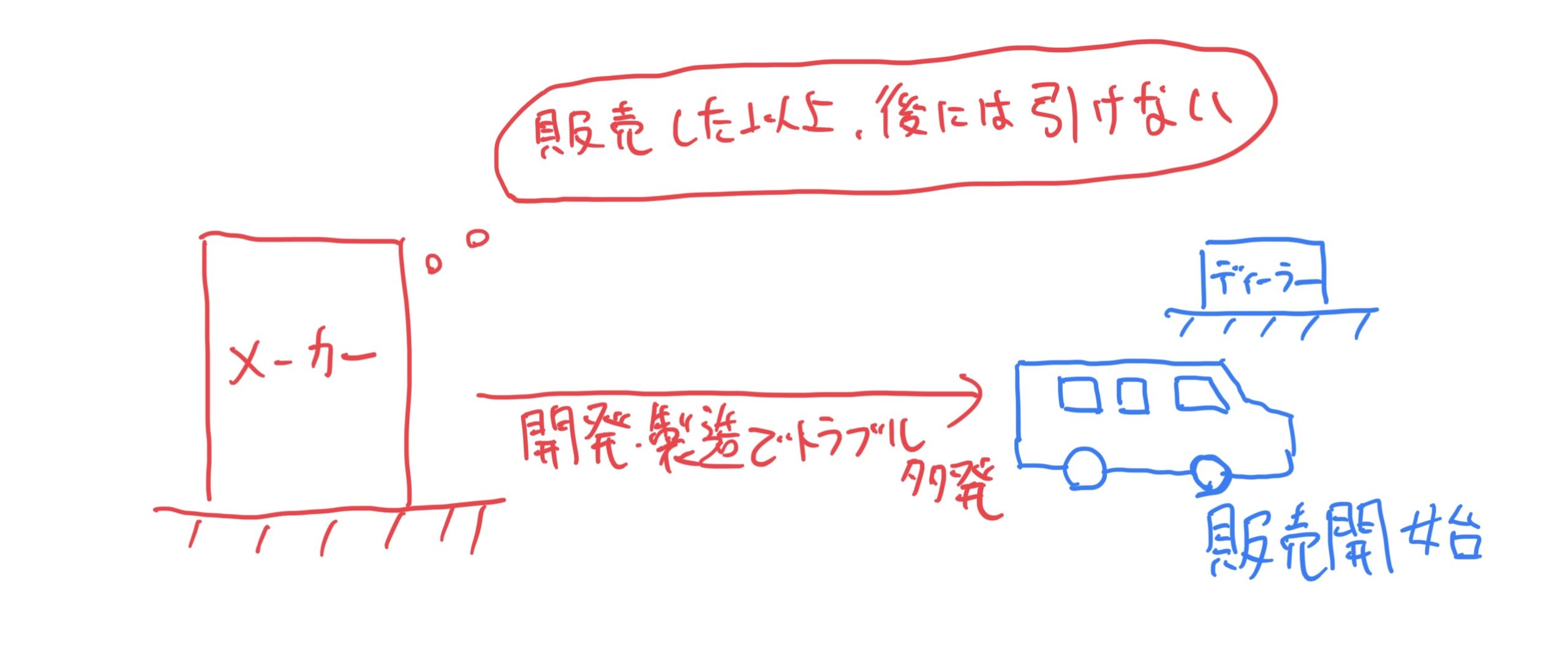
また新商品に不具合、問題があるとすぐに認めてしまうと、その性で過去に出していた商品も全て疑われたり、間違いがあったとか思われるのではないかと考えている節がある。
そんな感じで、とにかく認めたがらないし、やりたがらない雰囲気が現代でも蔓延しているのだ(ヤミ改修で対応してしまうことが多い)。
おそらくコメットの開発製造会社も同じ心理だったろう、しかも名門だからなおのことだ。
原因の特定は多くの時間、コスト、人間が必要になる大変なことなので巷で流行っている事件(機内火災)を基に一応の対応はしている。
これがまた良くないことで一応の対応をしてしまったので開発製造会社は、コメットがより完璧な機械になったと錯覚してしまうのだ(全然、意味がない対応でも)。
さらに良くなかったのが、その無意味な対応をイギリス政府が有効性を認め再飛行許可を出したことから益々、無意味な自信と自尊心が高くなるのだ。
本来ならば1件目の事故から即座に社内事故調査チームを組むのだがそれさえできず、最低限の実施するはずの開発内容、開発データのチェックすらしていない。
もし冷静になって開発内容のチェック、開発データの見直しをしていれば筆者が指摘した開発での問題点程度は、簡単に出せたはずである(筆者の100倍以上優秀なエンジニアが多く居たはず)。
もしかしたら筆者と同じような問題点に気づいた人達がいたとしても(実際にかなり存在したと思う)おそらく状況を見ると会社、政府のどちらも聞かなかっただろう。
もう早くコメットを営業飛行に復帰させることしか考えていないように感じるのだ。
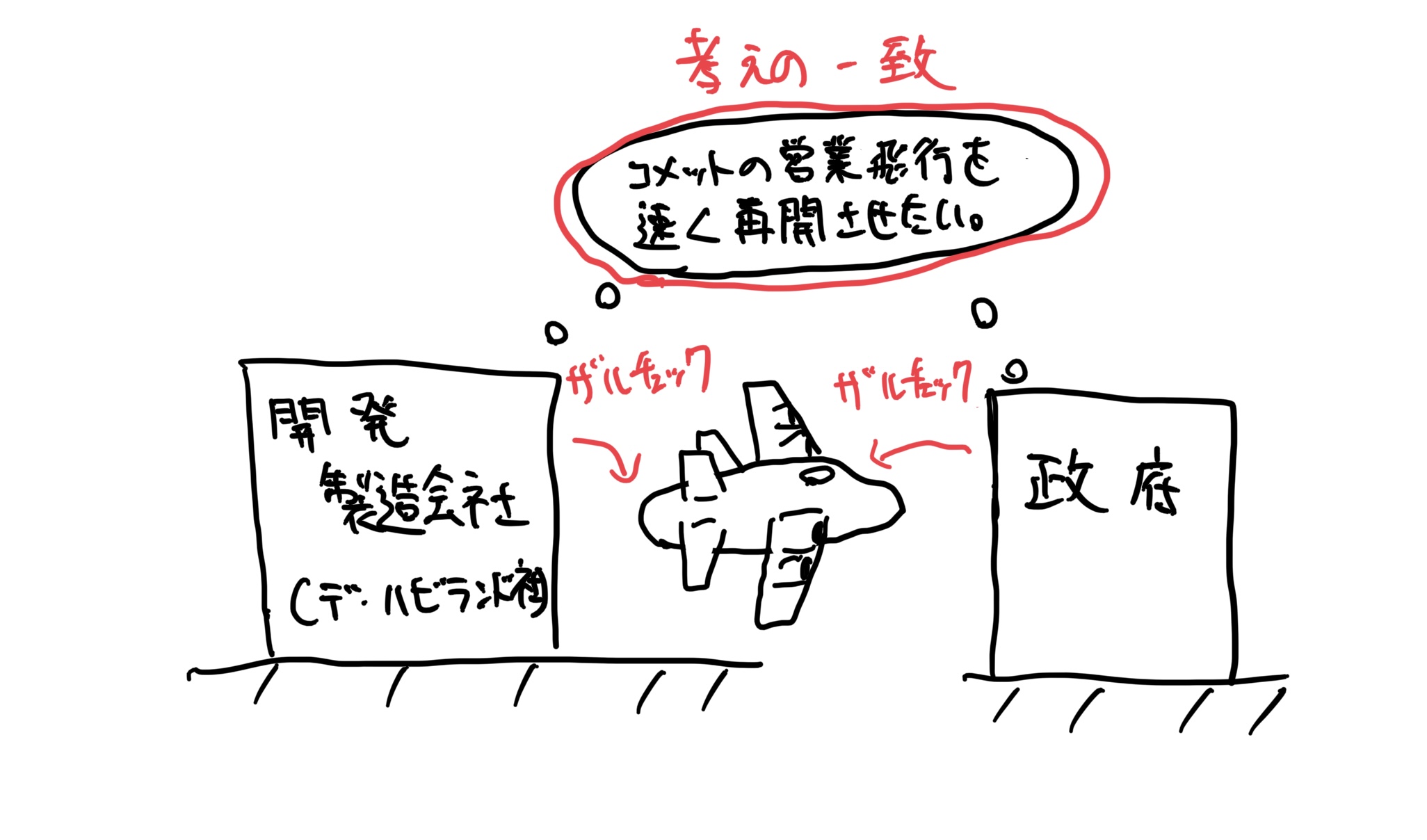
実は私たちの身近なところでも同じことが一昔前に起きていて国内大手自動車会社のHの3代目コンパクトカーFがトランスミッション(DCT)でおよそ6回以上(8回だったかな?)のリコールを出している。
おそらくリコールに至らない市場改修を含めると10件以上になると思う。
これも最初に大した問題と思わないで(原因探しをしっかりやっていない)適当なその場しのぎの対策を続けた結果、10回以上の対応をする羽目になり、お金と時間だけだけではなくかなりの信用を失ったのである。
次に3件目の事故を考えていこう。
3件目の墜落事故対応を考える 1954年4月8日 南アフリカ航空201便
3件目の事故対応を見てみると、政府と開発製造会社は、全く正常に機能しなくなっていたことがよくわかるし、正気かどうかすら怪しい感じだ。
開発製造会社は、1件目の事故をパイロットの操作ミスと悪天候などのイレギュラーが原因とした。
2件目の対応は、何故か飛行機の機内火災対策を行なって英国政府に認められ再飛行許可を取れた。
このような対応の後に3件目の事故が発生したので開発製造会社は、口裂けてもコメットに問題がある可能性を言えなくなった(この段階でも本人たちは、コメットに問題がないと思っているけれど)。
ここで機体コメットの問題があったかもしれないと発表すると、1件目の事故原因と2件目の対応がの無意味さを認めてしまうことになるからだ。
認めた瞬間、マスコミ達の餌食になる。
このように最初に間違えた対応をしてしますと後から修正するのは、とても大変かつ失うものがより大きくなるのでかなりヤバイのだ。
また政府もおそらく同じ状況になってしまって引くに引けないかなりヤバイ状況になっているはずだ(再飛行許可を出した手前、簡単に取り消せない)。
ここで政府が“コメットに問題がありました。“なんて言ったら国際的信用や航空業界に与える影響はかなり大きくなる。
この段階まで政府、会社が追い詰められると半狂乱的になり内部で少しでも方針に従わないことを主張する人がいると潰しにかかるくらいおかしな状態になっていることが多い。
まあ、どんな段階であれ本当は面子や直近の利益などを失うことを覚悟して、真実を追求、発表をしないといけないし(特に政府)、実は後から振り返ると正直にやり直した方が信用やメンツなどのダメージは、嘘で逃げるよりもよっぽどダメージは少ないものだ。
ここからは、運が良いことにあのチャーチル首相がいたので大きな決断をして利害関係がない人たちと大きな予算投入して原因は突き止められた。
特によかったと思う点は、利害関係になかったRAE(王立航空研究所)と英国軍を中心に動かしたことだ。
もう皆さんのお気づきの通り利害関係者になってしまった政府と開発製造会社は、もはや正常な動きができない状況に自ら陥ってしまった。
本来ならば相互チェックの対象である政府と会社という立場だったのだが利害が絡んでダメになった(コメットを速く飛ばしたい)。
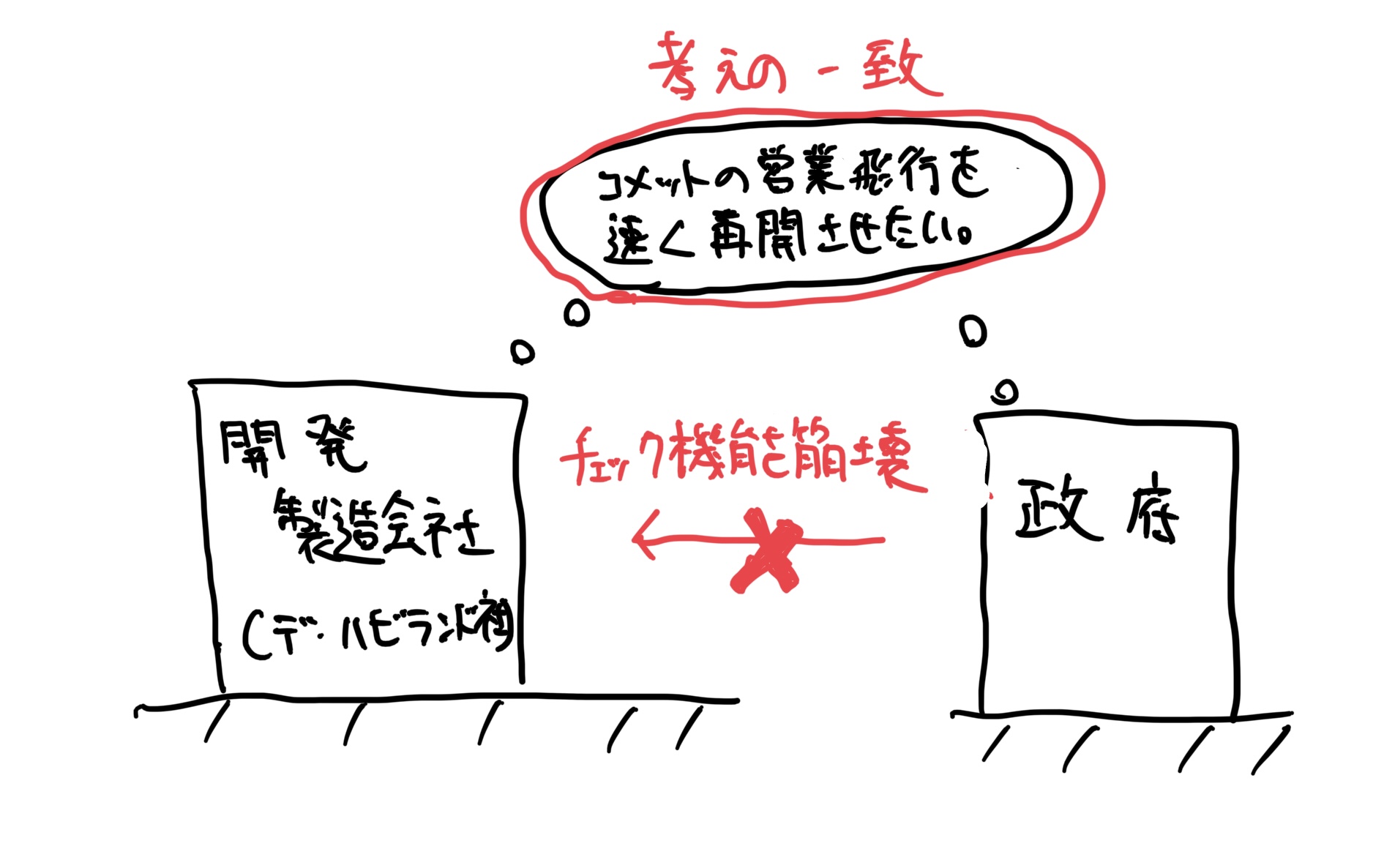
やはり正直な目、利害関係のないフラットな考えでやらないとまずいことになる典型例である。
ここでも企業倫理、技術者倫理が大きく関わってくるのだ。
結局、コメットの墜落事故の原因を掴んだのは、利害関係が存在しない第3者のRAEとなった訳である。
このように、本当は当人達(この場合で政府と会社)で解決、対応、対策ができれば良いのだが利害などから、おかしくなったらすぐに第3者に頼んだ方(RAE)が良いことがわかる。
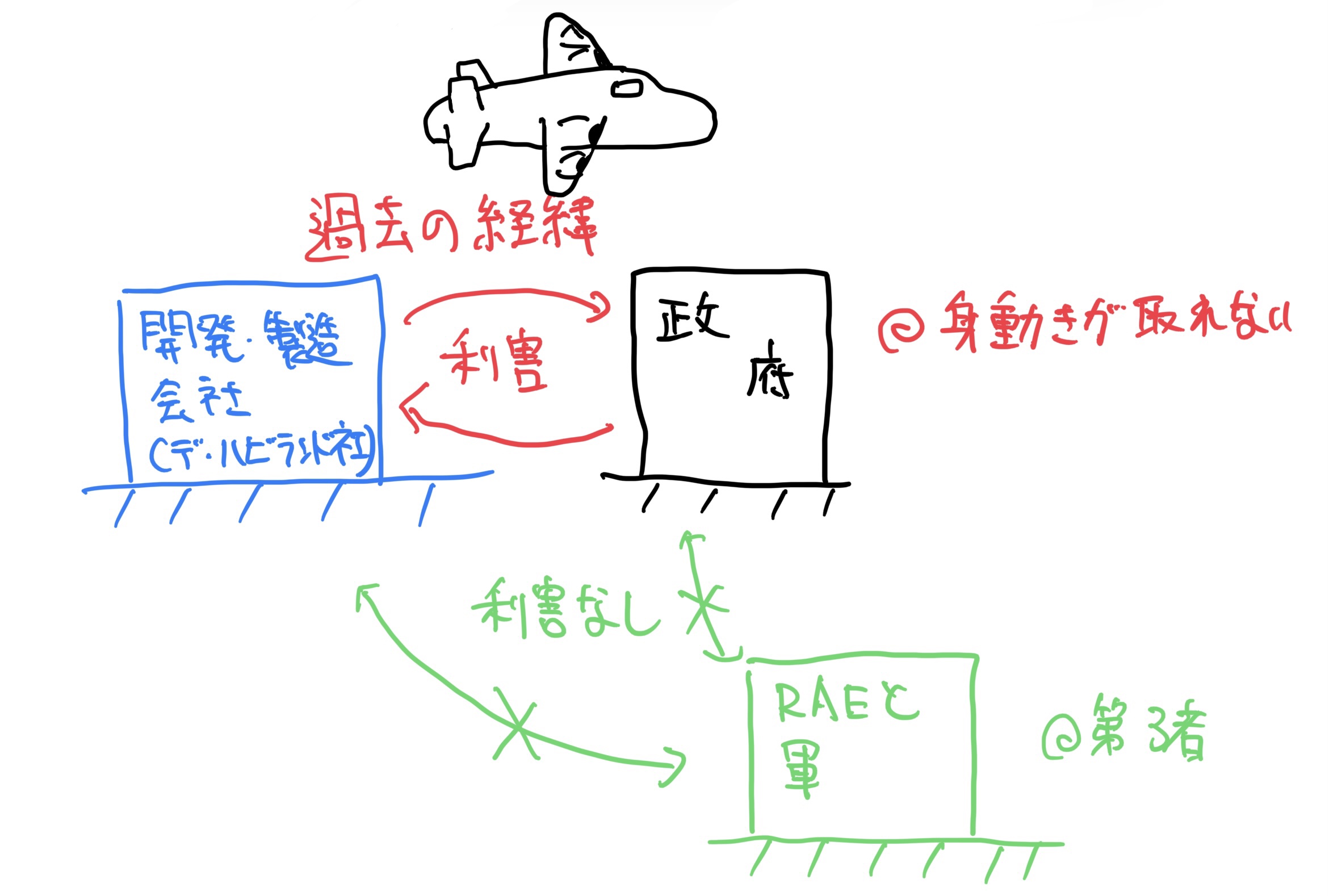
このような知恵は現代にも引き継がれ現代の日本でも課題があると政府はすぐに第3者委員会や有識者を集める。
この集まりが利害関係が無く集められていれば素晴らしいのだが、現実には完全に制度が形骸化していて、ただのお友達を呼んでいるように見えるので意味がない残念な結果になっている。
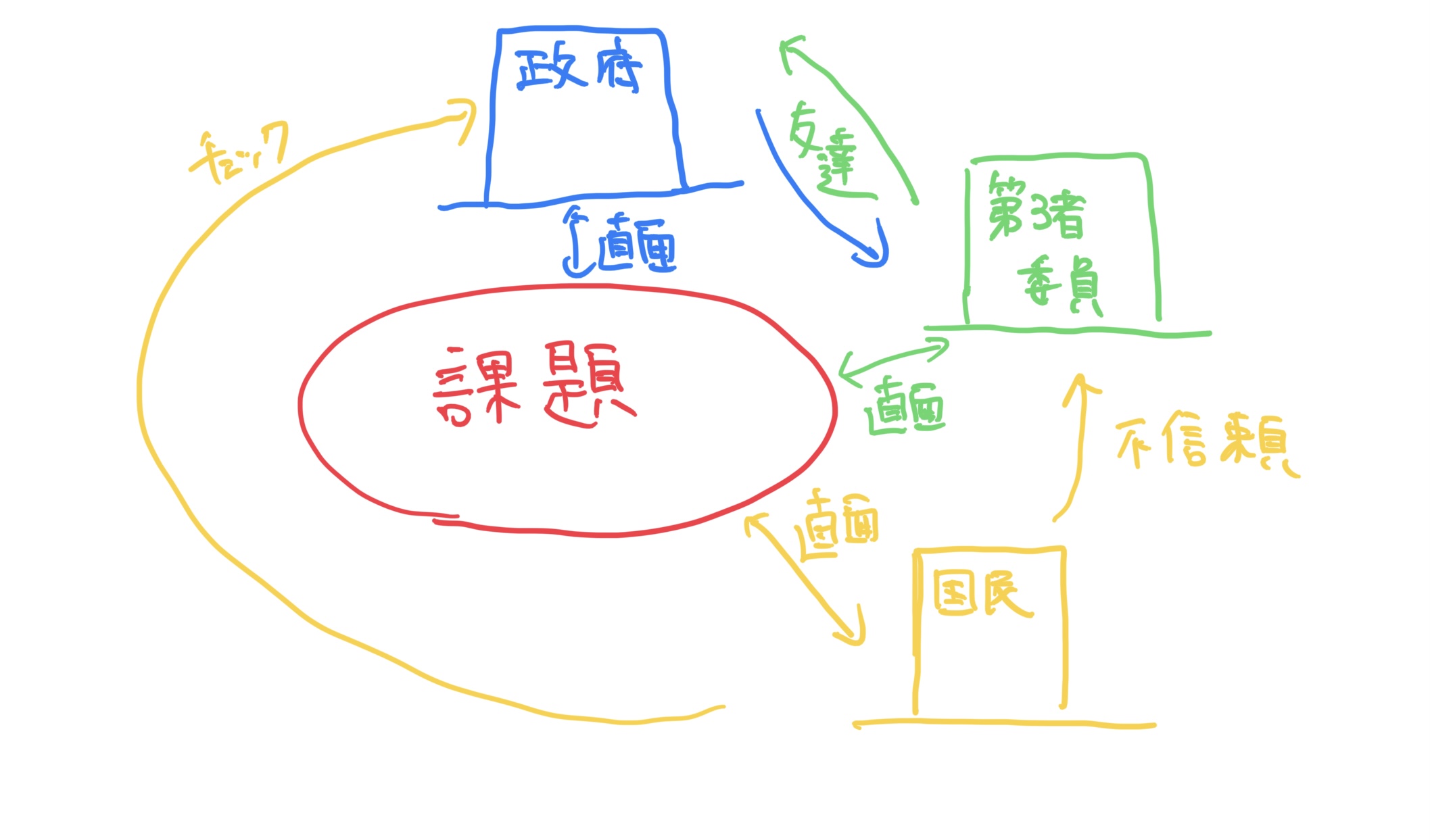
また企業でも経営に関しては、社外取締役(役に立っているのを見たことがない)みたいなのがいるけど現場、市場での不具合、事故に対応できる第3者機関の制度は、現代の日本には存在しない。
できれば経営だけでなくお客様の命を守る安全や市場不具合くらいは、歴史から学んで第3者による検証などの何かしらの仕組みをつくりたいものだ。
歴史から真の教訓を学んで実行するのは、とても難しいのである。
次回は、コメット墜落事故の原因再考のまとめと後書きになる。

ここでオススメしたいのがアマゾン キンドル アンリミテッドだ。アンリミテッドだと数多の本が月会費だけで読める(漫画〜専門書まで幅が広い)。
今回の記事で紹介したコメットの話が紹介されている名著、失敗100選などの本が安く読める。
しかも流石、本屋が原点であるAmazonだけあって機械工学の専門書がそこそこ揃っていてかなり使えるサービスだ。
特に機械工学の専門書は高額になることが多いので少しだけ読みたい分野の本を眺めるのに非常に役に立つので是非、オススメしたい。
折角なのでさらに機械設計で必須の本があるので紹介しよう。
はっきり言って中身は不親切極まりないのだがちょっと忘れた時に辞書みたいに使える。このブログを見てくれれば内容が理解できるようになって使いこなせるはずだ。
またよく使う規格が載っているので重宝する。JISで定められて機械材料の特性が載っている。
多くの人が持っていると思うが持っていない人はちょっとお高いが是非、手に入れて欲しい。但し新品は高いので中古で購入を考えている方は表面荒さの項目が新JIS対応になっているのを確認することを強くオススメする。
また本ブログをキッカケとしてエンジニアとしてステップアップして大きな仕事を掴む手段の一つとして転職するのも一つの手だ。
やはり予算の大きい機械設計、規模が大きい機械設計、大きな仕事をする場合は日本においては大手に入って仕事をする方がチャンスの機会が多いと思う。
私も最終的に転職はしていないが自分の将来を模索していた時期に転職活動をしていくつか内定を頂いたことがある。
折角なのでその経験(機械設計者の転職活動)を共有できるように記事に起こしたので参考にして頂ければ幸いだ。
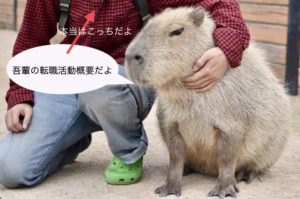
コメント