前回の紹介で古今東西で変わらない製品や機械の開発での試験、テストの基本的な考え方とコメットの開発時における一発破壊試験(限界荷重試験)について紹介してきた。
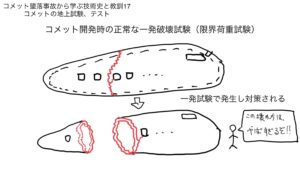
今回は、前回からの続きでコメット墜落事故の直接的な原因となった疲労破壊を確認する疲労試験に着目して考えていこう。
本題に入る前に皆さんに謝ることがあって今回は、今まで紹介してきたメカニズムの集大成になる部分で“以前の記事のリンクが多くなってしまったこと“と“疲労試験が製品、機械開発にとって最重要要素の大きな一つなので長くなってしまった、途中で切りたくなかった“ことを謝りたい。
ただ製品、機械開発だけでなく電気、電子製品を含めシステム、仕組みづくり、組織づくり、政策などのカタチがないモノづくりでも考え方の基礎になる部分なので多くの人に読んでいただきたい。
よろしくお願い致す。
まず、物体の破壊に関して一度の大きな荷重で破壊することを一発破壊と呼びある荷重が複数回に渡って加わった結果、破壊することを疲労破壊と呼ぶことは、以前の説明を参考にして欲しい。
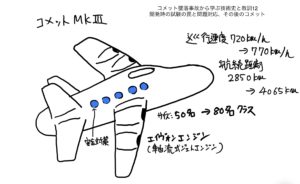
さらに詳しく知り合い方は、こちらを参考にして欲しい
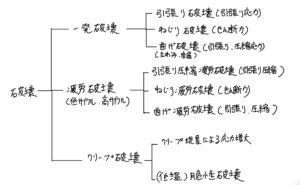
ここまでで前置きが終わったところでコメット開発時の与圧室の疲労試験を考えていこう。
コメットの与圧室の疲労試験
ここからコメットの与圧室の疲労試験について考えていくのだが、それ以前の問題点として一発破壊試験で使った部品をそのまま疲労試験で使ったことと与圧室を分割して試験を実施したことの難しさについては、こちらを参考にして欲しい。
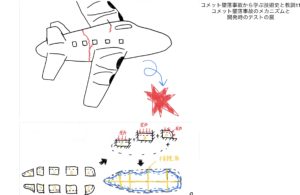
まずコメットでの与圧室の疲労試験の問題点を考える前に古今東西に関わらない通常(正常な)の疲労試験の流れを少し説明する。
一般的な疲労試験
この疲労試験は前回で説明した試験、テストの流れの中で最後の耐久試験の中に入る試験で、さらにその耐久試験の中でも一番、最後に行われる超重要な試験になる。
疲労試験を実施する前に想定した全ての機能、性能を確認し、一発破壊試験(限界荷重試験)で単純な耐久性を通過して始めて実施できる最後の試験になる。
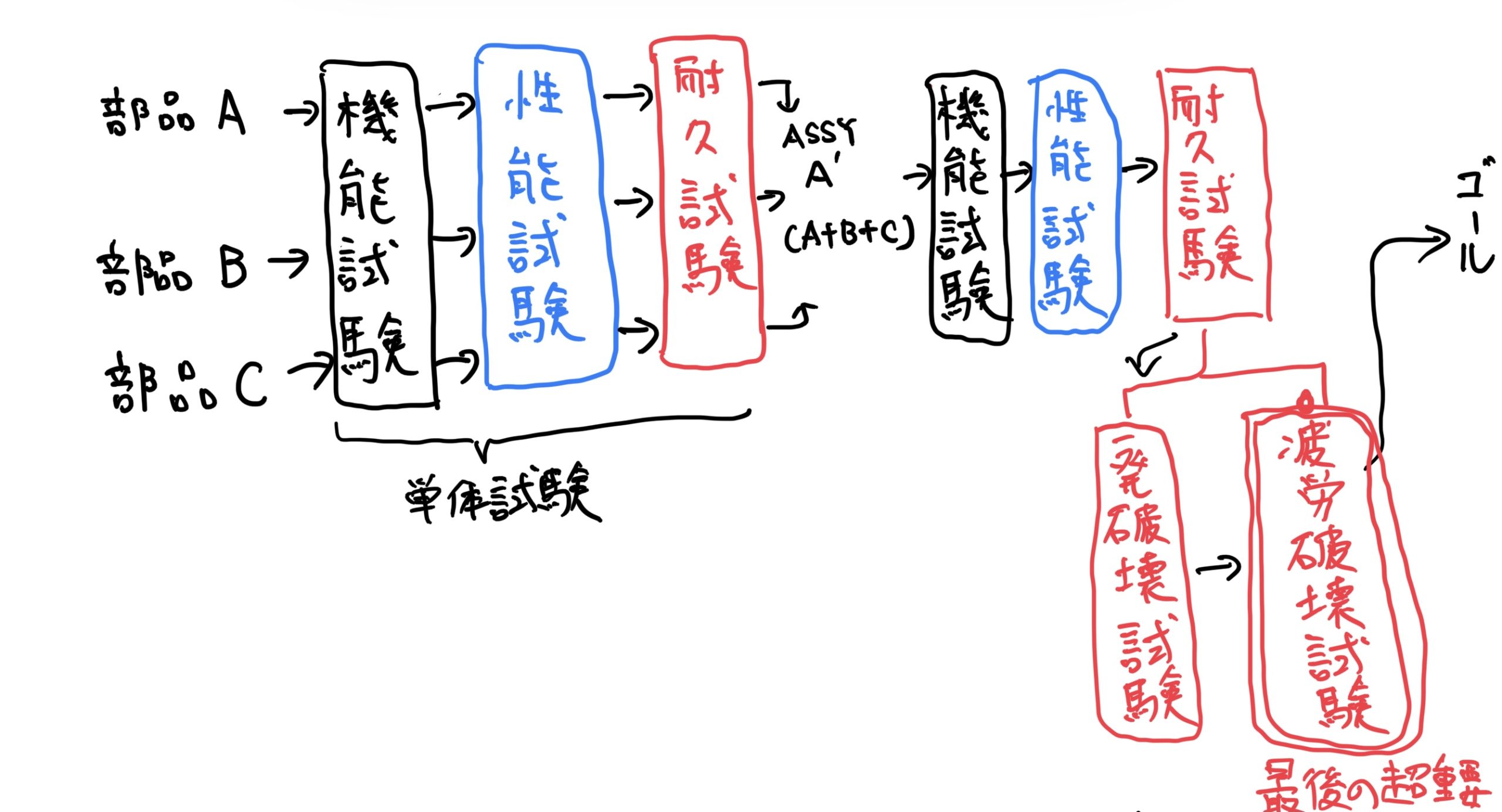
また疲労試験の基本的な考え方は、試験対象の部品が$ 10^7回$(機械における大切な寿命の目安)の負荷に耐えることを確認する試験になる。
実際には、$ 10^7回=1000万回$もの荷重を部品に与えることは効率や時間の面から現実的ではなく、実際にはその会社が持つノウハウや経験値に加え信頼性工学を使って試験時間を濃縮する設定や条件(与える荷重の大きさ、時間などを複雑に変化させる)で試験を行う。
それでも疲労試験は、筆者の感覚だと最小で3〜4日間で長い試験になると3〜4週間くらいの時間がかかる場合もある。
しかも単純な部品、例えば図のような金属片に単純な引張り荷重が複数回に渡って加わるだけならあまり難しくないが、機械は複数の部品から構成されており複雑に力が絡みあって(引張り、圧縮、ねじり、曲げなど)条件がかなり複雑になってくる。
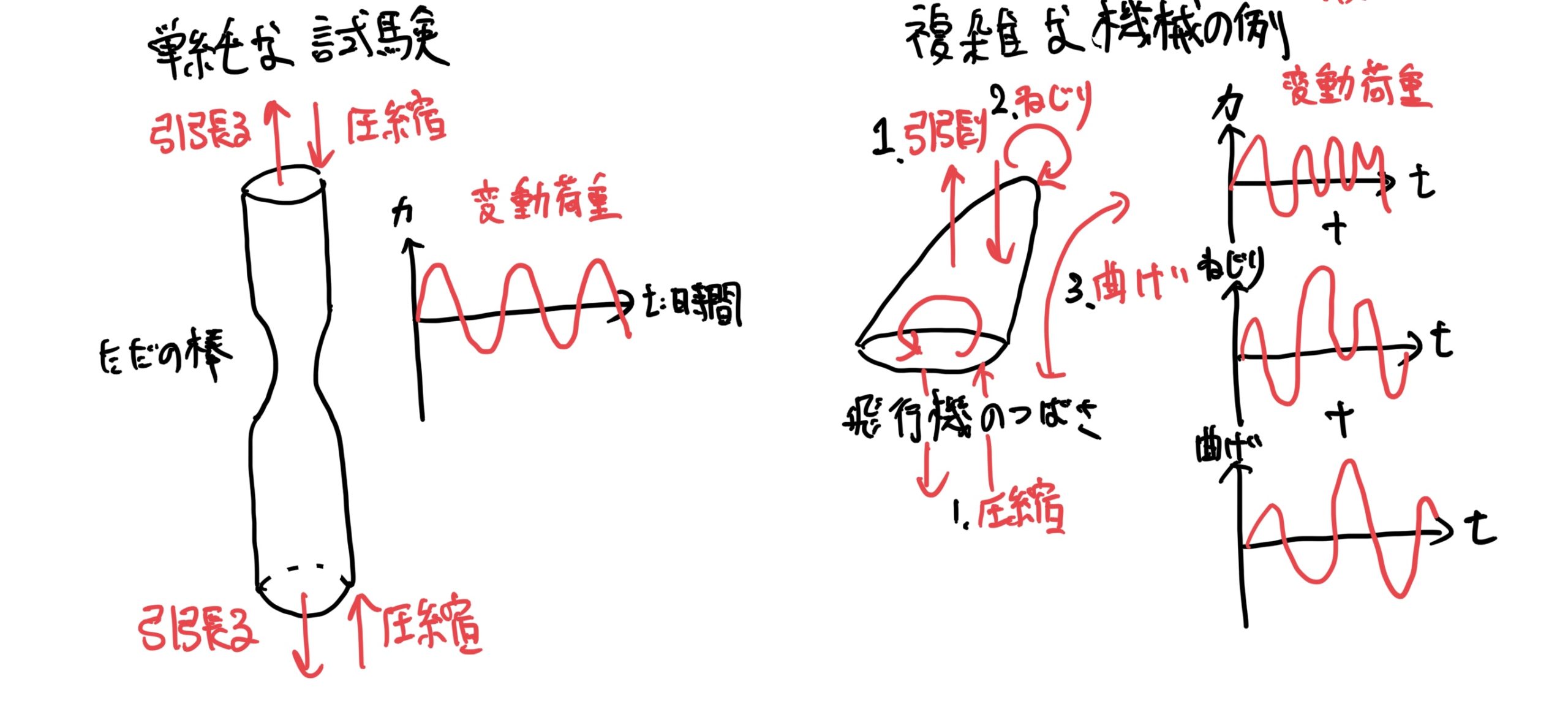
つまり疲労試験の条件の設定は、超難しいのだ。
このような処理を経て作成する試験を一般的に複合耐久試験(又は、単純に耐久試験)と呼ぶ。
この複合耐久試験を経て“市場で使われても十分な寿命を持つ、その寿命の途中で不具合を発生しない“と見做して量産されるのだ。
つまり、まともな工業製品ならば“この複合耐久試験を実施されないで販売されている製品は存在しない“と言っても過言ではないくらい重要なのだ。
さらに複合耐久の試験条件や内容は、各企業や団体で異なっておりその内容は、超重要機密事項になる。
場合によっては、同じ会社でも部署が異なるけで複合耐久の内容を知ることができない場合ですらあるくらいだ。
つまり複合耐久の内容は、その企業や団体のこれまでの様々な失敗、市場の実績、経験を基に作成されているノウハウの塊で宝物なのである。
複合耐久試験の雰囲気(自動車のエンジンの耐久試験)
実際に複合耐久の雰囲気を筆者の専門分野の自動車のエンジンで具体的に説明する。
自動車のエンジンの仕事は、単純に考えると加速、減速(エンジン回転上昇、エンジン回転下降)の2種類になる。
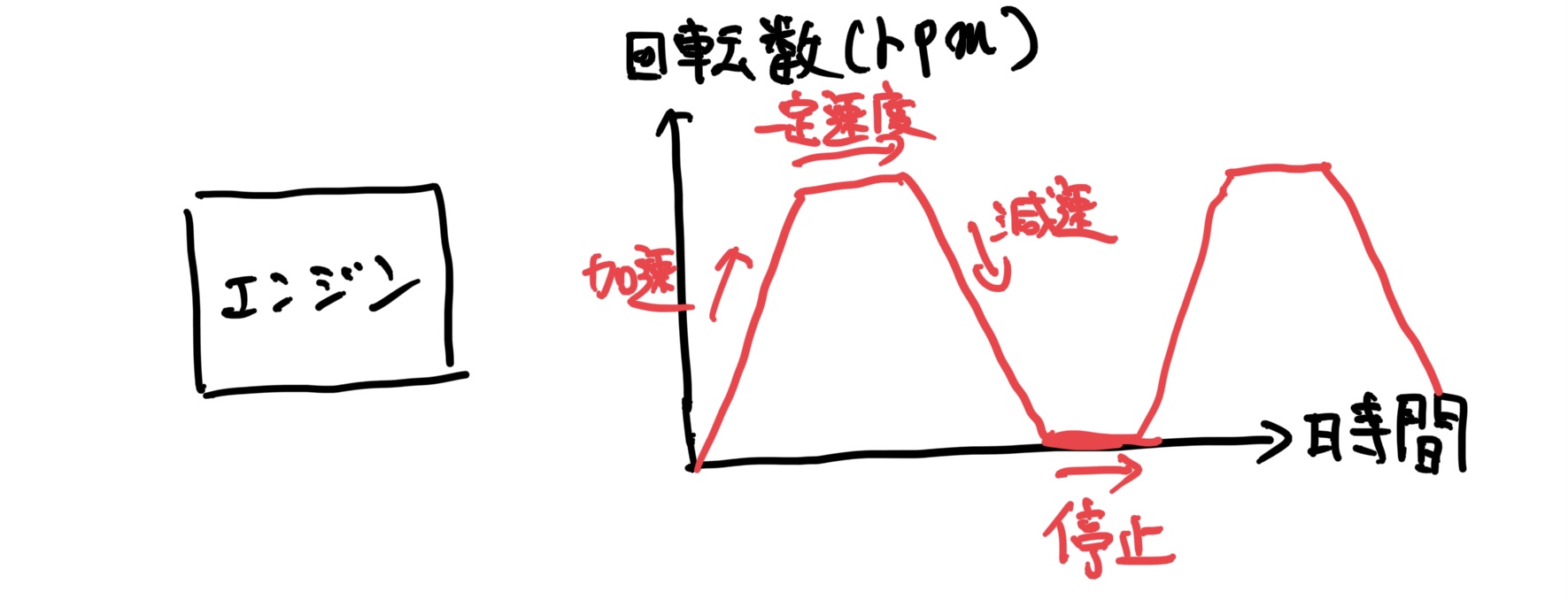
しかし実際の自動車の使われ方をみると緩やかな加速、急な加速や一定速度の運転などが複雑に絡み合う。
わかりやすく言うと例えば渋滞のノロノロ運転や急いでいる時の急発進、急加速、急減速、急停止や高速道路での一定速度での連続走行などがある。
さらに海外事情まで考えるとインドネシアの超過密渋滞からヨーロッパのアウトバーンでの平均時速200km/hオーバーの超高速連続走行まである。
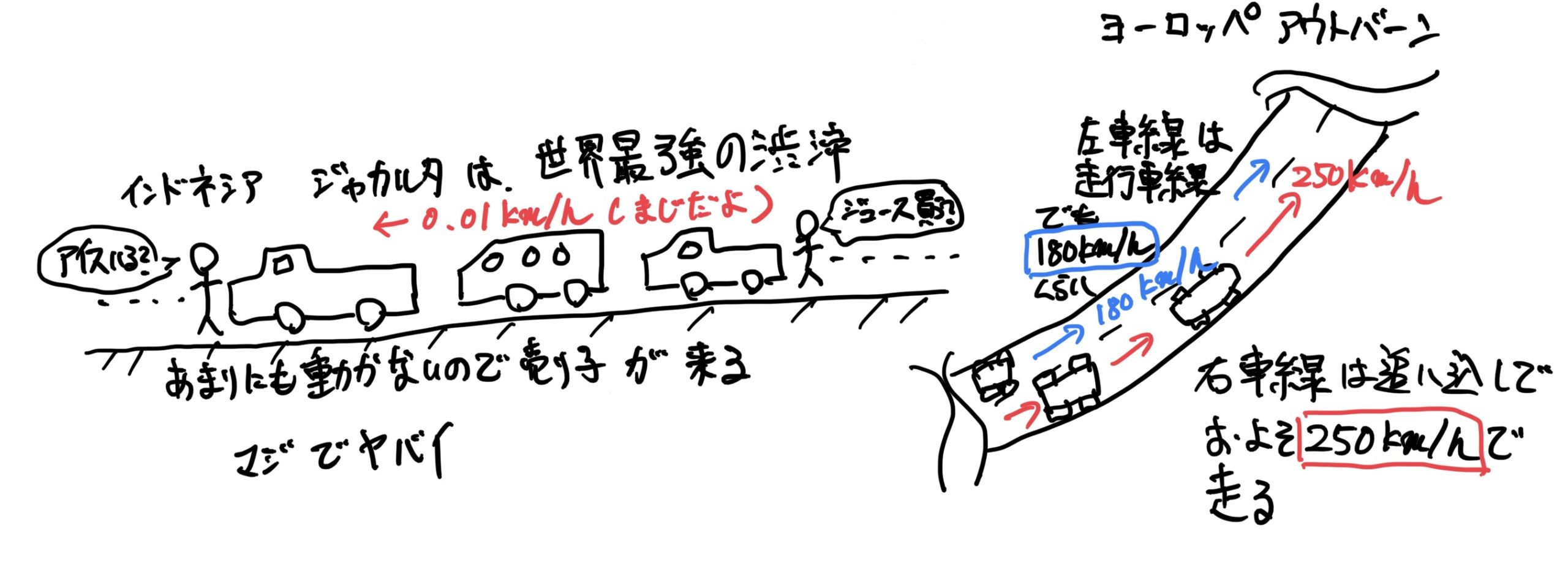
特殊な用途の自動車だと例えばスポーツカーだとそれらに加え峠走行、サーキット走行なども加わる。
これらに加えエンジン自体による負荷だけではなく、例えば自動車が段差を乗り越えたときの衝撃やカーブでの横Gなどの外的要因による負荷も考慮しなければならない(ヨーロッパの石畳道路や進展国の未舗装道路など)。
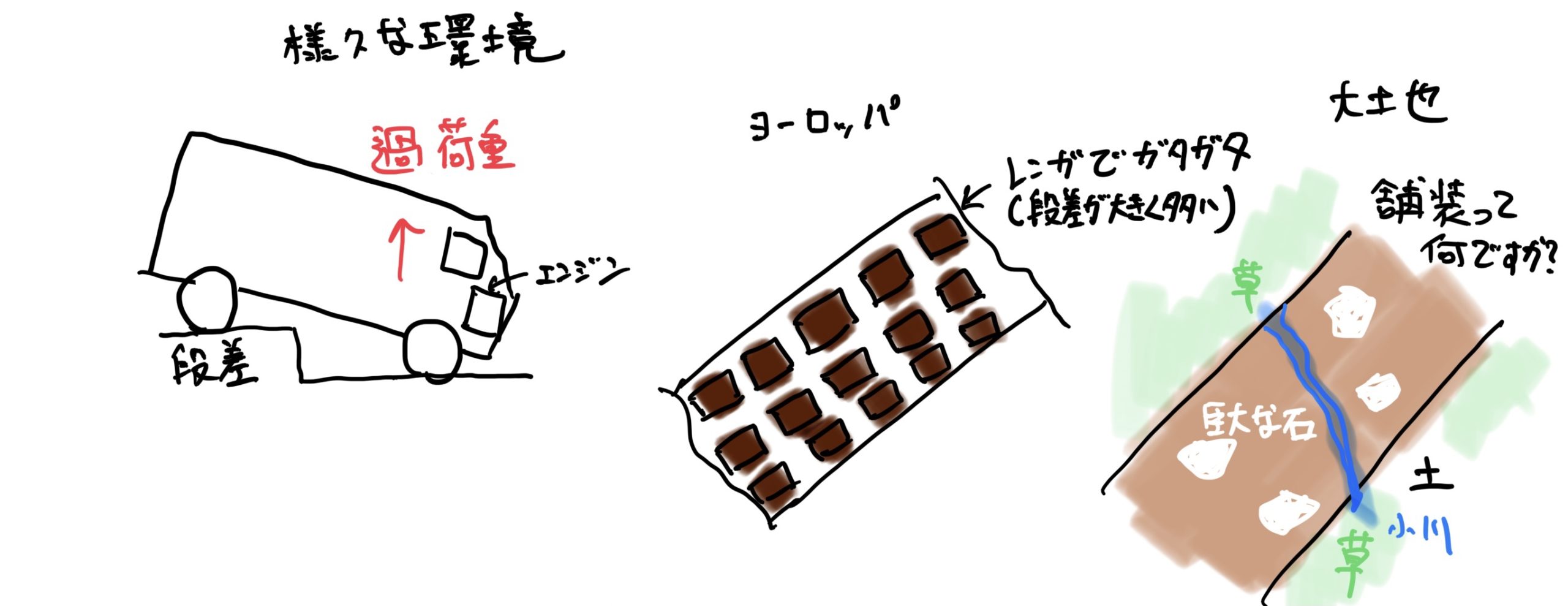
これらの使われ方を考え得る全ての事象を絞り出し、企業が持っている量産実績、ノウハウ、実走データを総合して決められるのが複合耐久になる。
少し脱線するが多くの人が知っている自動車レースの最高峰のF1のエンジンの複合耐久では、各サーキットの実走データを基に複合耐久でほとんど実際のレースと同じ負荷がかけらるような装置が一昔前からできている。
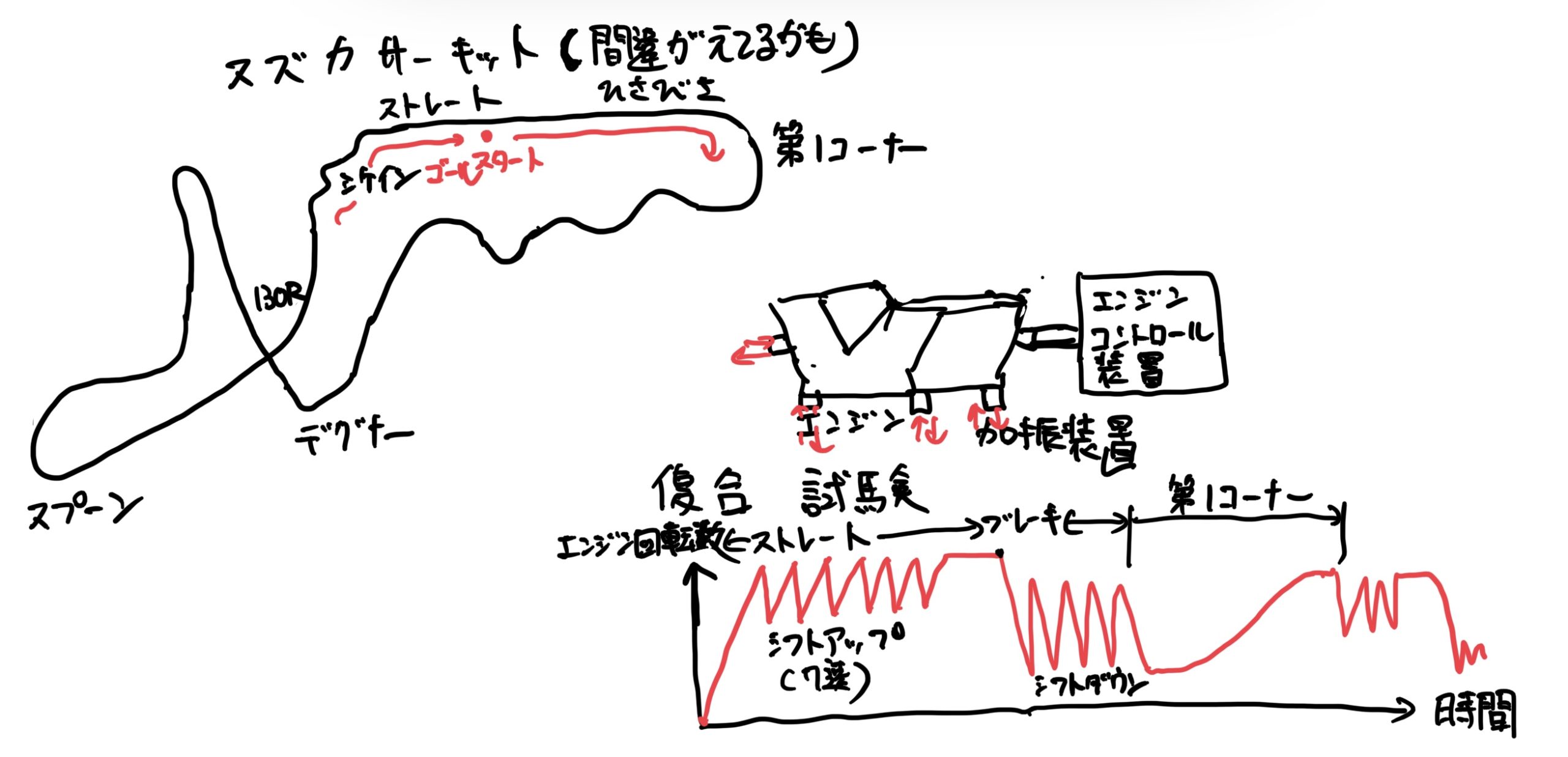
さらには、ドライバーのクセも再現する。
例えばある人は、ブレーキとアクセルを同時に踏むクセがあったり、ミッションのシフトアップ(ギヤチェンジ)する時にアクセル全開のままだったり、考えられない場所でアクセルを急に抜く人がいたりする。
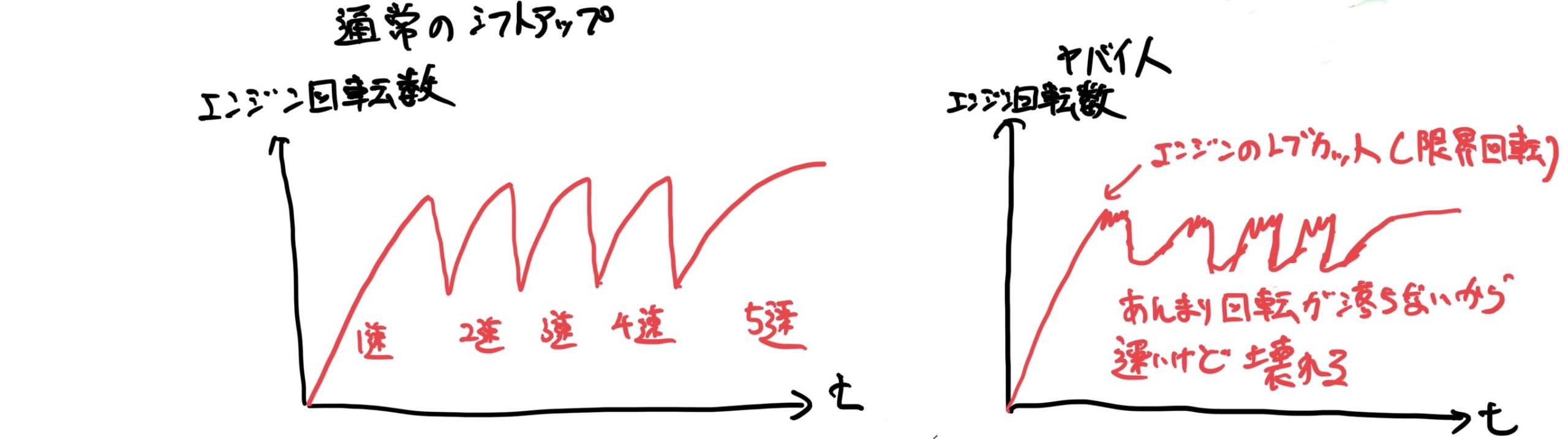
こんなクセすらも複合耐久の条件に入れる場合もある。
筆者もレースエンジンの開発をしていた頃は、ドライバーのデータ(エンジン回転数の変化、アクセル開度、加速度、G変化)と睨めっこしながら考えて設計をしていた時期もあった。
データだけでは、わからないこともたくさんあるので実際にドライバーに聞いたり、レース現場に行って実際の車両の挙動とモニターに写し出されるデータを見ながら考えたりしたこともある。
ここまでやってもやはり新しい製品、機械には、それなりの新しい現象、予想外の使われ方などが発生して残念ながら不具合が出ることがあるのだ(新しいことは、難しい)。
複合耐久の基になる実測データ、実走データの重要さ
もう一つ重要な視点があってカンの良い方は、お気づきかもしれないが、ここまで説明した複合耐久に必須の条件は実走データ、量産実績、ノウハウなどの経験値なのだ。
当然ながらレースも自分たちで出場しない限り正確な実走データを得ることは、ほぼ不可能に近く、大抵の場合は、一年目はかなり苦しい(いくらテスト走行距離を伸ばしても実践には、敵わない)。
どんな天才が考えても、シミレーションがどれだけ発達しても限られた空間、ルール、条件で走るレースですら精度が高い複合耐久を作成するのは、かなり難しい(ほぼ不可能)。
ましてや、様々な人々が様々な環境で頻繁に自由に使用されることが多い乗用車などは、条件が複雑すぎて超難しい。
ある意味では、誤解を恐れずに言うとロケットなどの超限定的かつ超プロフェッショナルだけが使用し、厳密に管理されている機械のが複合耐久の観点だけで考えるとかなり楽だ(日常生活で皆さんがいつも使う機械ほど開発が最も難しい)。
つまりいくら理論やシミレーションなどが発達しても実際のデータ、ノウハウがないと複合耐久は、絶対に作成できないのだ(実際にやってみないとわからない)。
実は量産品の設計もどんな検討、シミレーションよりも実測データ、実走データのが比較にならないくらいありがたい存在なのだ。
人間の行動を含めて自然法則には、まだまだわからないことがほとんどで理論上で可能であっても実際に使うとなると、そこには超大きな壁が立っている。
その壁を乗り越える道具は、2021年の現在でも経験、実測データに勝るものは、ほぼ存在しないのだ。
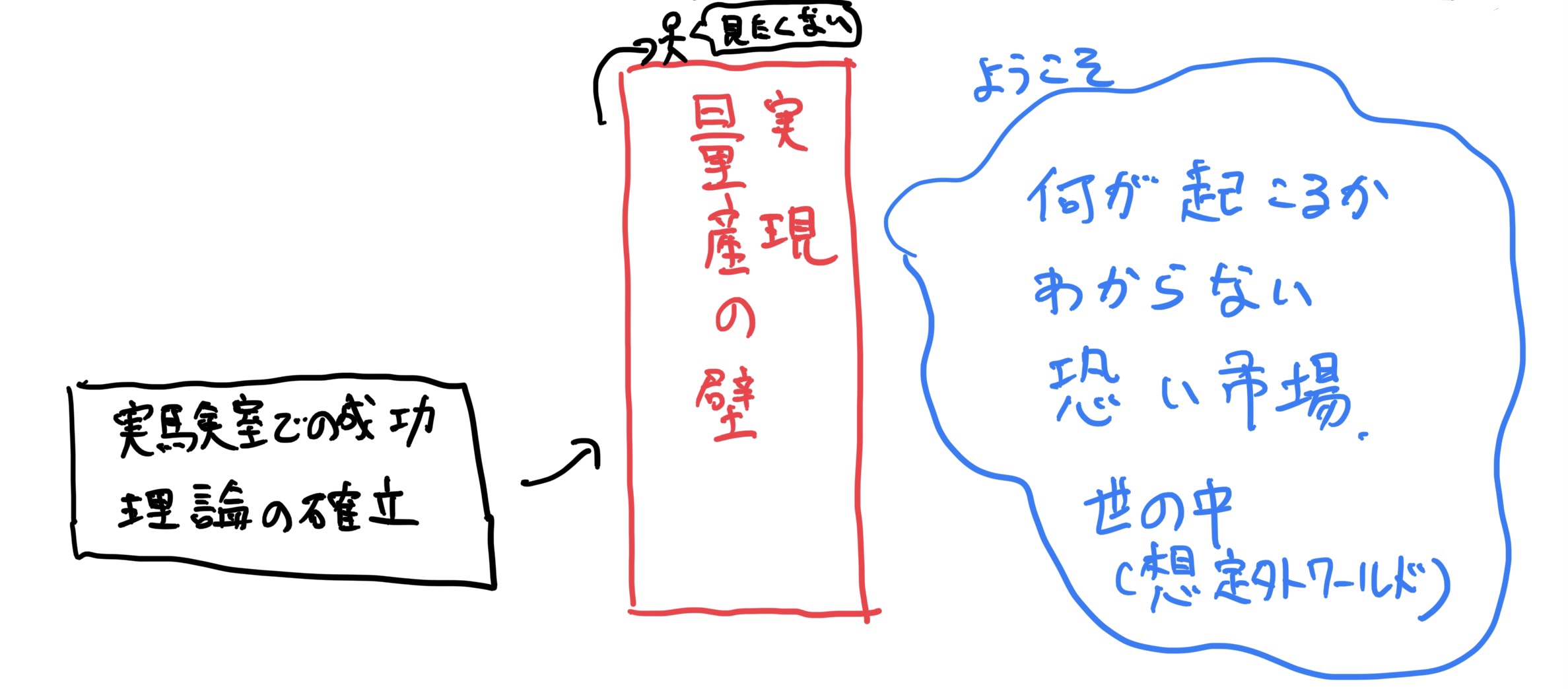
この難しさを身近な例で考えると最近時の流行りの電動自動車や自動運転などは各技術要素(モーター、バッテリー、レーダー、AIなど)がそこそこ成熟していても、実際にそれらを全て組み合わせた自動車の量産の走行データ、実測データ、ノウハウが圧倒的に不足しているのですぐに実現できそうに見えるがなかなか実現しないのである。
また電気自動車で考えるとモーターやバッテリーに詳しい電機会社がすぐできると思う方がいるかもしれないが、その電機会社には残念ながら実走データ、実測値、ノウハウがないのでどれだけ各技術要素(モーター、バッテリーなど)に詳しくても、すぐに安全な自動車を生産することは、ほぼ不可能に近い。
そもそも、無謀にもいきなりよくわからないメーカーが電気自動車を発売しても危なくて乗れたもんじゃない。
だからと言って新規参入のすべたがダメと言うわけではなくて、新規参入する場合は、十分に量産することの難しさを把握してできる限りの知恵と努力をして量産に近い走行データをどれだけ獲得するのかが勝負になってくるのだ。
だからグーグルなんかはアメリカのカリフォルニア州政府と協力して自動運転車両を一般道でバンバン走行させて実測データを取っている。
どんなに高度な装置、巨大な実験設備やスーパーコンピューターで代替しようとしても実走データ(実測データ)には、敵わないのだ。
つまり工学やものづくりは、$ \frac{2}{3} $くらいは経験に基づくことが占めていてノウハウ、量産実績、量産データが超重要になるのだ。
実はここもでで何度も述べているがこのような実走データ、ノウハウの基づく複合耐久の精度、内容の濃さなどのレベルは、経済だけでは、わからない企業の実力そのものになる(不具合が多いメーカーは、ノウハウが少ないことが多い)。
産業発展、イノベーションのための政府への筆者のアドバイス
筆者程度のエンジニアが日本政府の政策の“多くの自動車の電動化“の実現に対してアドバイスするならばお金の投資や減税をするだけではなくて、国土交通省、警察や公安などと協力して多くの試作の電気自動車を走行させる特区や多くの人が乗れる環境を整えて参入メーカーに実測データ、実走データ、実績値などを蓄えさせないと実現は、かなり厳しいと思う。
筆者の考えではメーカーの本音は、お金や減税よりもその実測データ、実走データ、実績値のがよっぽどありがたいと思う(ある意味での限定的な規制緩和)。
実際に日本の最大の自動車会社(世界一といっても過言ではない)でも日本の行政では、許可が出にくいので自動運転車両のテスト走行は、アメリカのカリフォルニア州に試作車をわざわざ持って行って走らせている(本当は日本でやりたい)。
筆者も試作者の公道での走行データ集めのため許可を取ろうとしたら国土交通省、警察庁、公安委員会、経済産業省に加え地方の公安委員、警察、行政との調整が必要でめんどくさすぎて断念した。
手続きが面倒なのと時間がかかる割には、走行許可される条件があまりにも限定的すぎて得られることも少なそうだったのも理由だ。
海外だとヨーロッパであればEUの交通局で許可を貰えればEU内でどこでも走れるしアメリカの特定の州では、むしろウチの州でやってくれとセールスされるくらいだ。
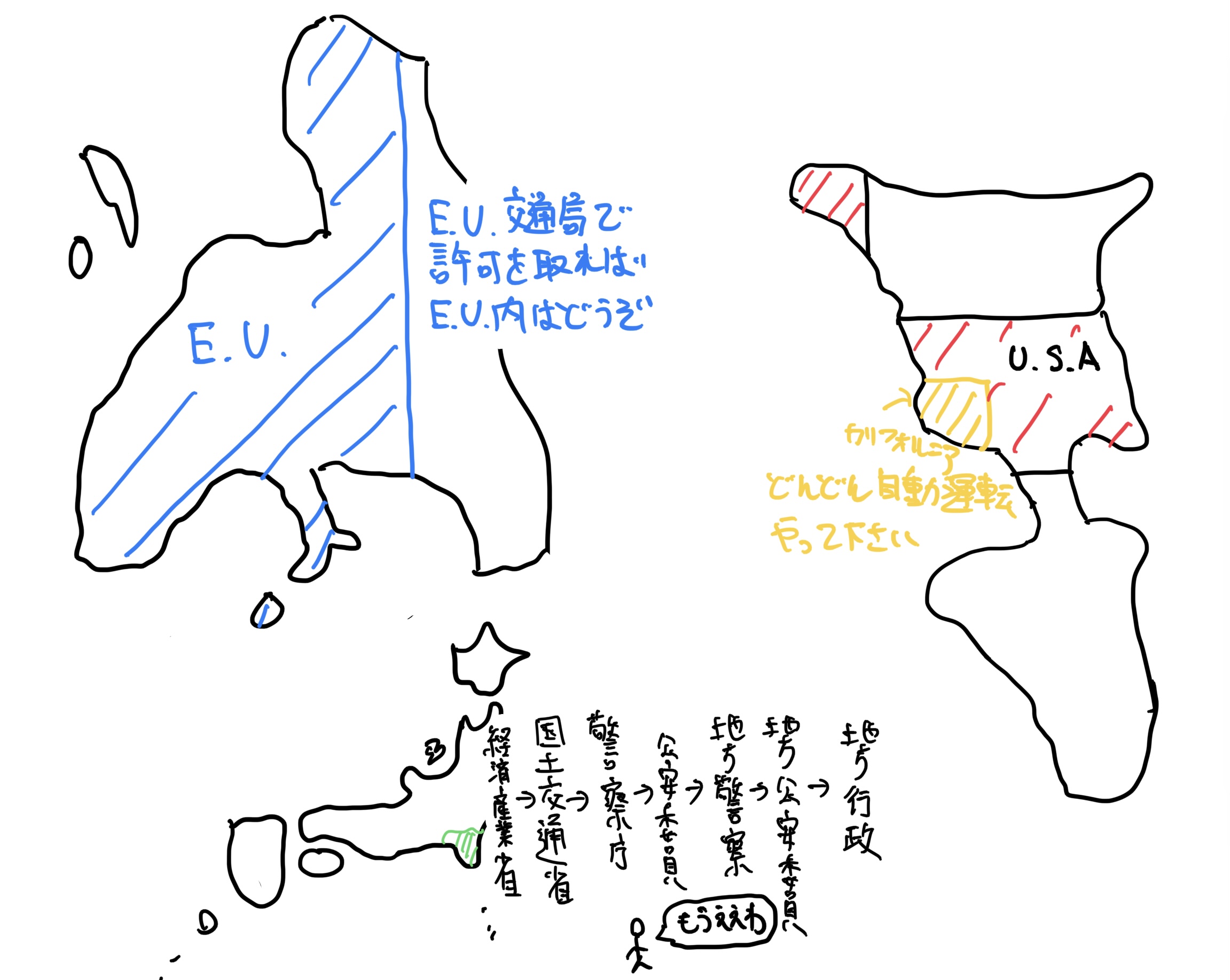
つまり現代の日本の政策や縦割り行政では、イノベーションを起こすことは、かなり難しいと感じる経験をした。
これは自動運転などの自動車だけでなくロケット、軍事衛星や戦闘機の軍事兵器から民間輸送機器などの複雑な機械や社会を変えるようなモノの実現には、必要不可欠なことだと思う(限定的でもいいから規制緩和、技術特区など)。
と少し長く書きすぎたがそれだけ重要な要素であることを理解していただければ幸いである。
やっとコメットの与圧室の疲労試験を考えていこう。
コメットの与圧室の疲労試験
コメットの与圧室の疲労試験も上で説明したように開発、製造会社のそれまでのノウハウ、実飛行データ、実績値(旅客機や戦闘機を生産していたのでノウハウとデータはある)から条件が考えられて疲労試験を行なったはずである。
もし単純に与圧室に圧縮空気で一定圧を加えて取り除くだけの試験だったらとしたらかなりヤバイ会社である(流石にそんなことはないと思いたい)。
仮に一般的に言われている“与圧室内に想定負荷の0.56[atm]を加え、安全のために1000回に一回の割合で2倍の1.12[atm]を加えた“の条件だけで疲労試験を本当に実施されていたとしたら開発製造会社にこのような命に関わる機械を開発するレベルにないと考えざろう得ない(実際はもっと複雑な条件のはず)。
ここからコメットの疲労試験の実施について考えていこう。
上でも説明したように疲労試験は、かなり重要な試験で会社や政府などの注目をかなり集めるイベントなのだ。
コメットの与圧室の疲労試験の様子
注目を集めると言うことは、疲労試験の条件などや疲労試験の実施の様子も設計図面と同じレベルの厳密なチェック体制が取られるのが普通で企業や団体である。
筆者の話で申し訳ないがエンジンの最後の試験はエンジン総合複合耐久みたいな名前で実施され、筆者程度の設計ですら試験中は会社に出勤したら、自分の席に行く前に毎日、必ずテスト室に行ってエンジンが壊れて試験が止まっていないか?試験中の各データに異常はないか(油圧、水温、馬力など)?などを自分で確認してから自分の職場に行った。
流石に設計の管理職がテスト現場に毎日、行くことはないが筆者は、必ず試験の状態を上司に報告していた。
それこそテストの担当者は、1〜2時間おきくらいに見に行って、ちょっと変だなと思ったら試験を一旦、止めて各部品や試験設備をチェックすることもある。
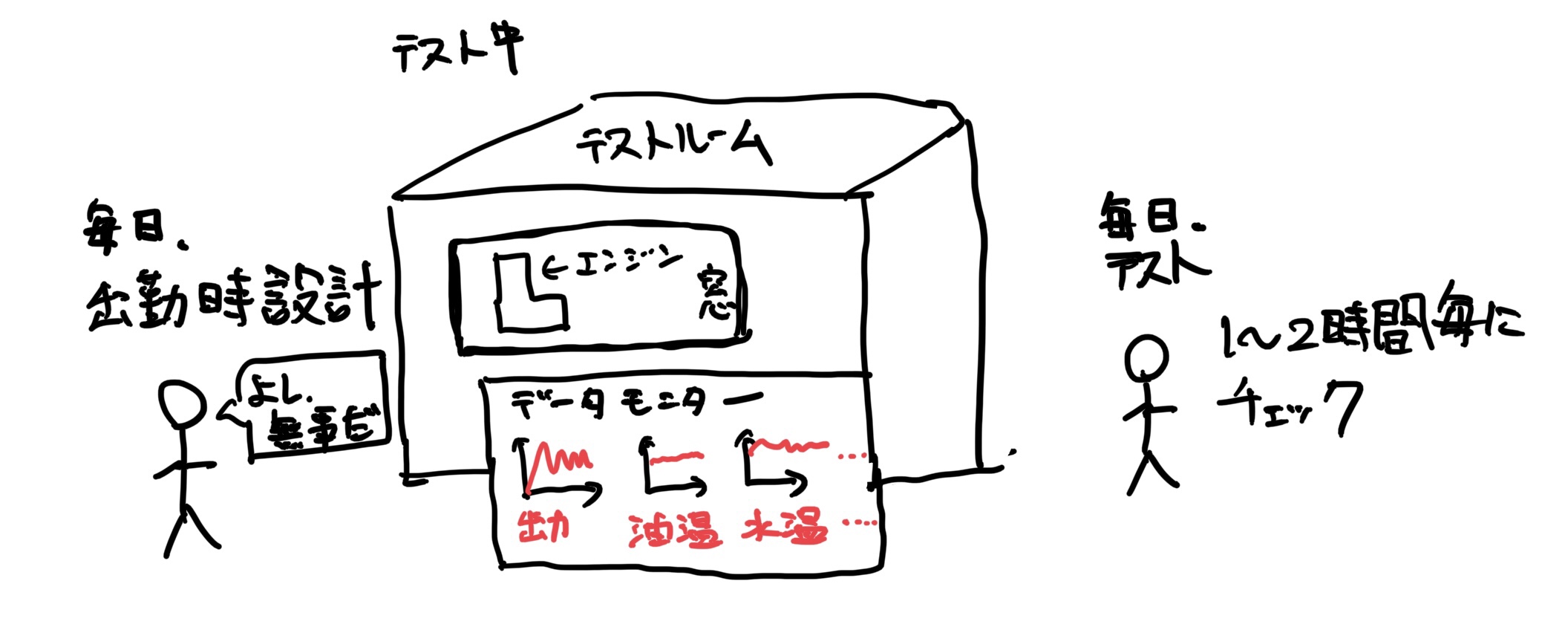
さらに開発するエンジンに新機構などのチャレンジ要素がある場合は、異常がなくてもある時間毎に試験を止めて部品の目視チェックを入念に行い微小な亀裂、破壊を見逃さないように相当、気を使って進めるのだ。
つまり試験されている部品、試験設備のどちらでも異常が出たら即、わかるようにするのが当たり前である。
しかしながらコメットの与圧室の疲労試験について、このような当たり前のチェックが行われた形跡が見当たらないのである。
少し遠回りになるがコメットの開発時の与圧室の疲労試験で発生していた事象を説明する。
コメット墜落事故の開発時の試験の罠で紹介したが開発試験での落とし穴の一つである圧縮残留応力を思い出して欲しい。
確かコメットの与圧室の疲労試験の条件は膨張と圧縮を1000回繰り返しの1回の割合で想定負荷の2倍の荷重を与えていた。
その2倍の荷重により圧縮残留応力が発生して実際の強度より強くなってしまったと説明した。
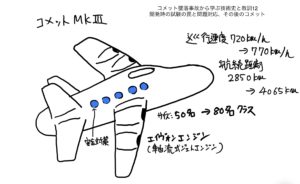
これをもう少し詳しく説明すると実は、開発時の疲労試験でも窓の角やアンテナ穴に亀裂が発生していたと考えられるのだ。
ただし、その亀裂が成長して与圧室の破壊に至る前に試験の圧縮力によって亀裂が潰されてたまたま破壊に至らなかったようだ。
つまりコメット開発の疲労試験の途中で窓の角やアンテナ穴に亀裂が発生していたのである(破壊に至らないだけ)。
当たり前の試験の管理体制が敷かれているならば説明した通り担当者レベルでも頻繁にチェックをしているので試験中での亀裂を発見することは難しいことではない。
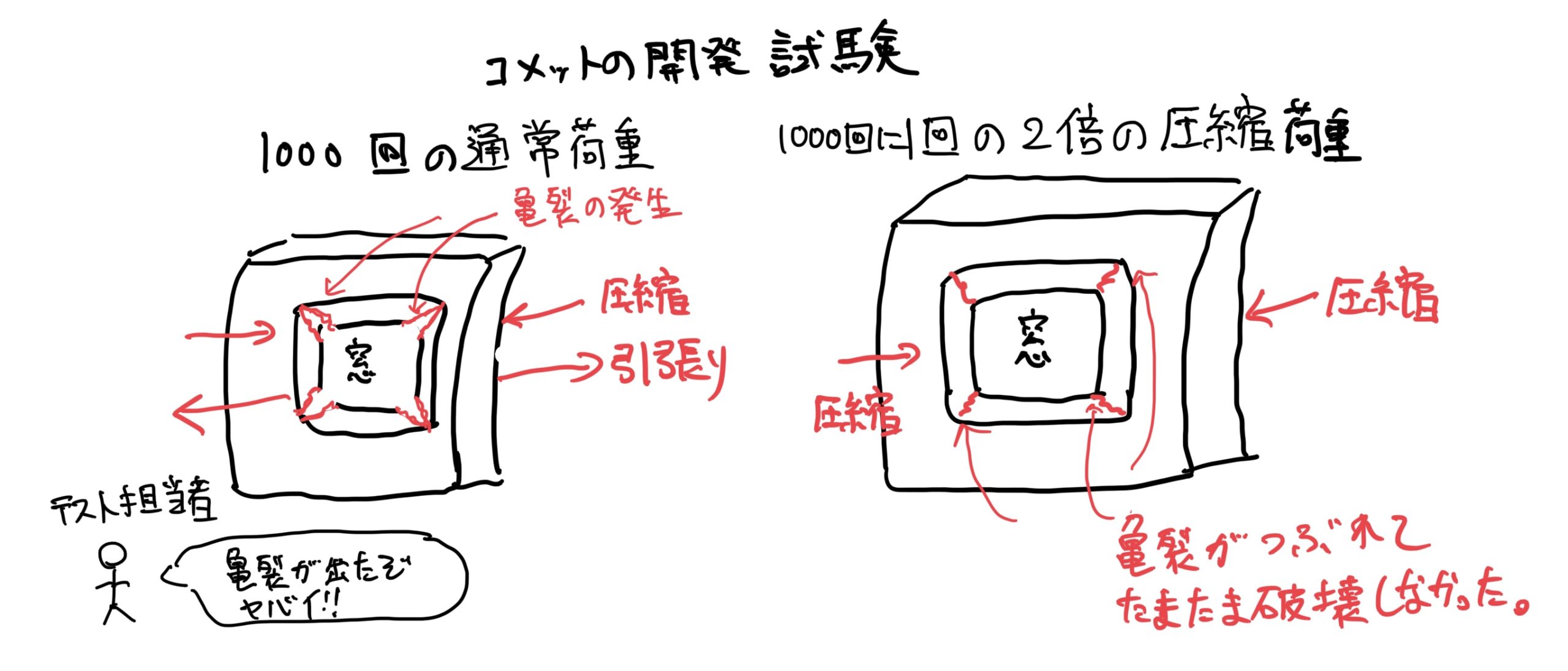
もしくは担当者は、真面目に亀裂の発生を報告しても時間がないことや焦りから上司連中が壊れてないから別に良いと握りつぶしたかのどっちかだ。
さらに一発破壊試験を正常に行なってれば100%の確率で窓の角やアンテナ穴に応力集中して与圧室が輪切りになって壊れるのがわかるので疲労試験の時に窓の角やアンテナ穴などの部位は、かなり厳重かつ短い時間毎に多くの人によるチェックをするはずだ。
ましてや、コメットは世界初のジェット旅客機の開発なので筆者が経験した自動車エンジンとは比にならないくらいの新規性、チャレンジ性があるので普通の感覚ならば与圧室の疲労試験は、かなり皆が気を使っているはずである。
ここで何が言いたいのかというと疲労試験の途中で発生したアンテナ穴や窓の角の亀裂に気付かない、発見できないという事象があり得ないのである。
疲労試験が終了した与圧室のチェック
また仮に試験途中のチェックを実施していなくても、このような疲労試験が終わった機械は完全に分解して、各部品に以上がないか入念にチェックする(特に亀裂の有無には、かなり気を使う)。
さらに人間の目視チェックでは見落とす可能性があるので特殊な溶液を使うと亀裂に色が着いて浮き出て見易くなる作業を行う(浸透探傷試験、クラックチェック)。
特殊な溶液と書いたが別に入手性に難があったり、価格が高かったり、最近できたものでもなく昔からある溶液で現在ならば探せばホームセンターに売っている。
この溶液で全ての部品を染めて微小な亀裂が発生していないか全てチェックするのだ。
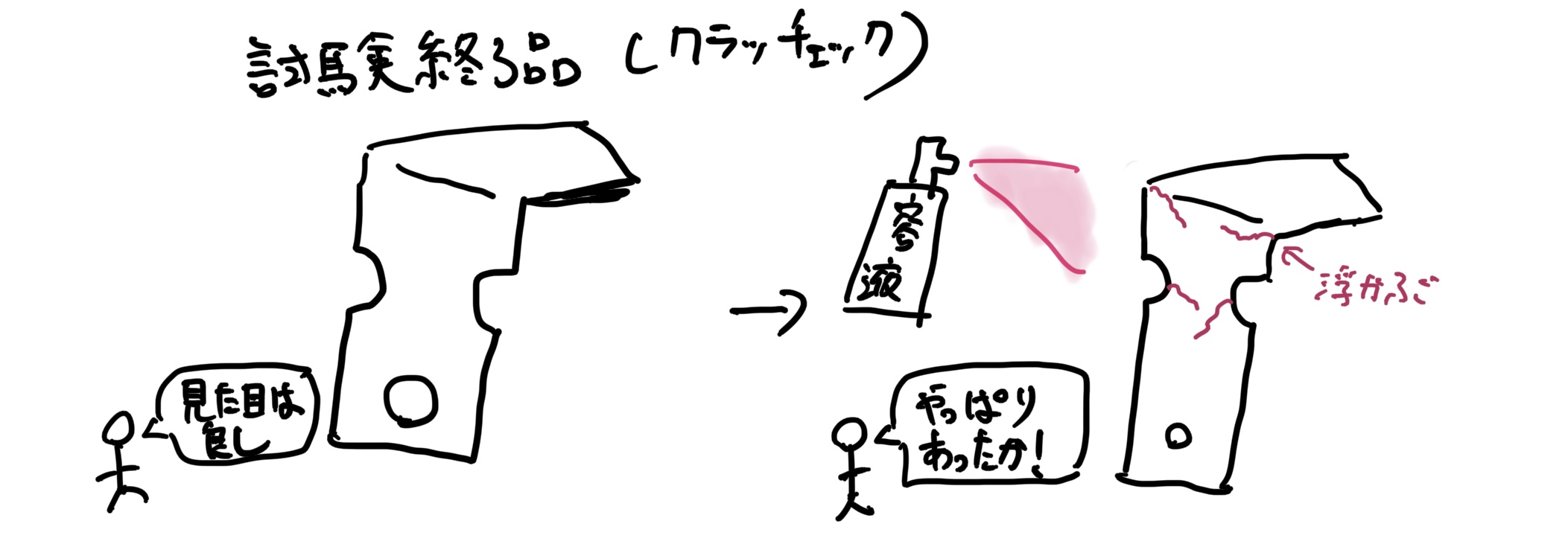
これに加え設計時に決めた応力集中しそうな箇所や怪しいところは、見た目がなんともなくても内部亀裂が発生している可能性があるので材料の専門家が部品を丁寧に切って亀裂の痕跡やは破壊の起点の跡がないかを顕微鏡で入念にチェックする。
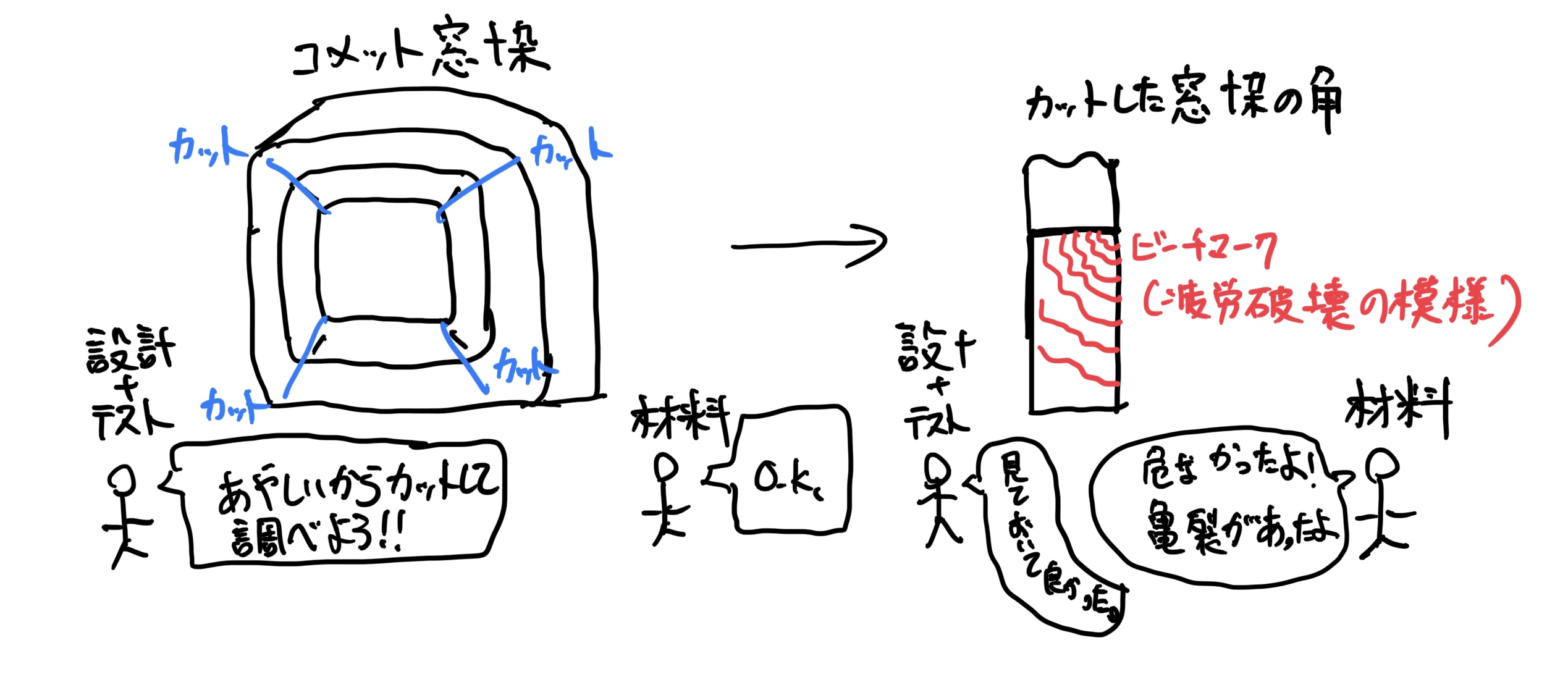
ここまでやってもまだ見落としの可能性があるのでより多くの人に見てもらうために分解して染めた部品やカットして調査した部品を全て展示をして部長、課長クラスは、もちろんのこと開発スタッフの全員が見れる展示会を行うのだ。
場合によっては、これだけの重大プロジェクトだと技術担当役員が見にきても不思議でないくらいのプロジェクトだ。
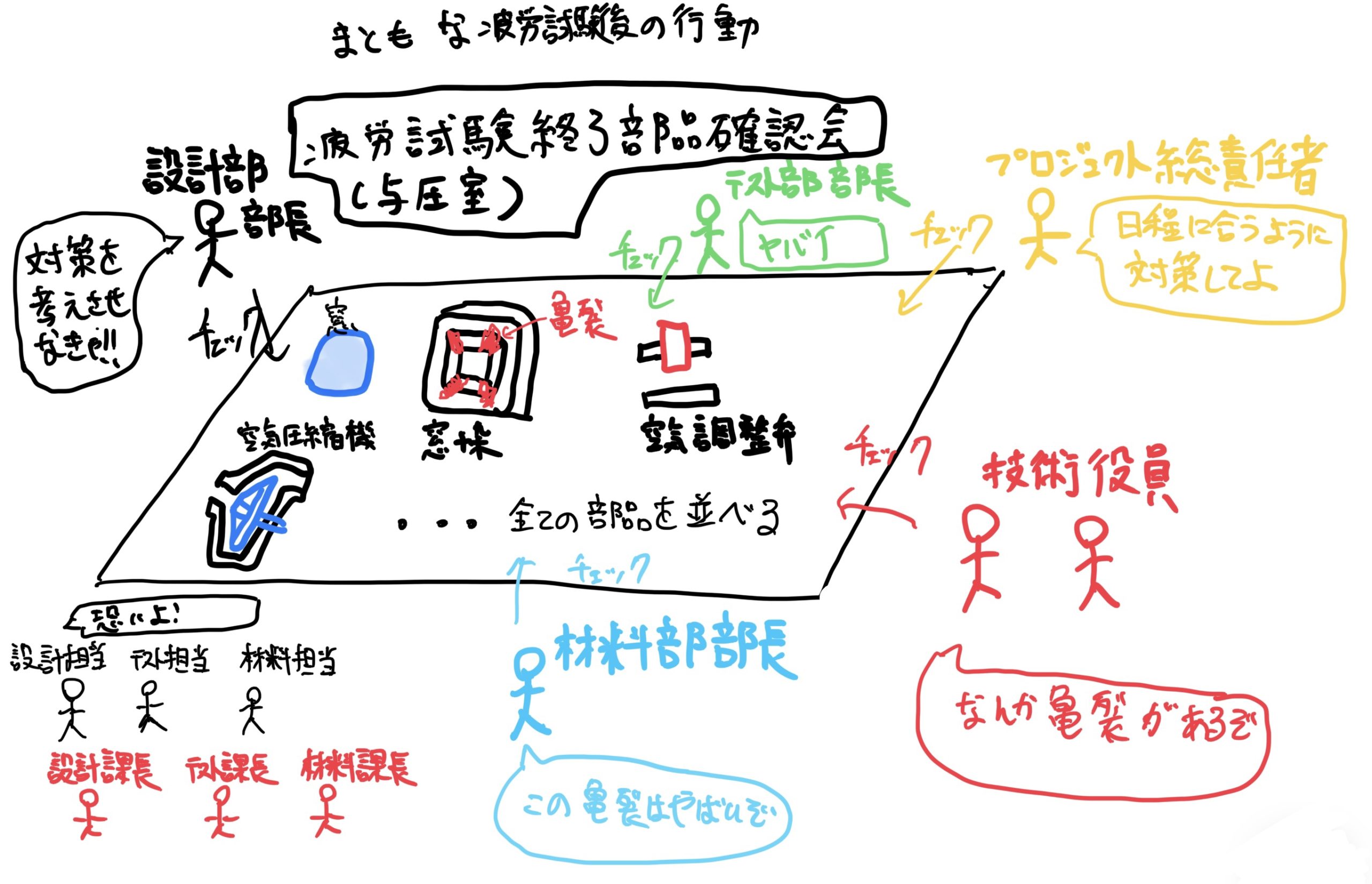
ここまでやってなんともない場合のみ試験完了で量産に向けて次のステップに進めるのが普通だ。
つまりコメットも仮に試験中に亀裂を発見できなくても試験終了品の調査を普通に行なっていれば100%発見できるのだ。
いくら亀裂が圧縮荷重によって潰されたとして外から亀裂が見えなくても部品をカットすれば必ず形跡があるのだ(材料は、正直で変化があれば痕跡を必ず残す)。
もう一つコメットのこの段階での筆者が考え得る致命的なミスは、試験が終わった部品の調査で亀裂が発生していたものの与圧室全体が破壊に至らなかったとして試験クリヤしてしまった可能性がある(言い方としては亀裂が入ったものの進展なしで問題なしというヤバイ判断だ)。
これは機械にとって一番、やってはいけない判断で部品に亀裂が発生していると特定方向の荷重には、ある程度、耐えるが違った方向による荷重には滅法、弱い部品になってしまうのだ(亀裂があるのだから当たり前)。
しかも一度、亀裂が入った部品は、壊れる様子が正常な部品と異なって亀裂を起点に猛烈なスピードで速度で破壊が進みバラバラに破壊されてしまうのだ(分解現象、木っ端微塵)。
つまり、たまたま試験でかけた荷重、負荷の方向だと亀裂が入っても与圧室が耐えられただけで、亀裂が入った状態で実際に飛行した際に突風や乱気流などに巻き込まれ想定外の方向から少しの荷重が加わっただけで急速にかつバラバラに破損する可能性が非常に高い危険な状態なのだ(ちょっとの外乱で空中分解する可能性が大)。
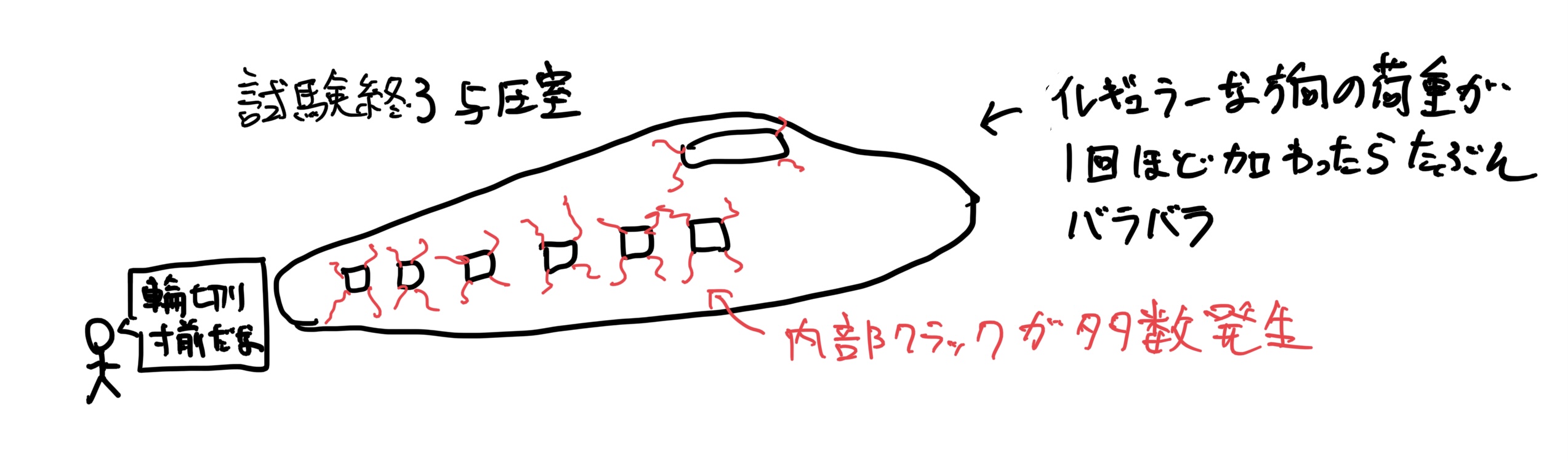
身近な例だとガラスのコップ、花瓶、鉢のなんでも良いが単純に落として割れた場合は、2つか3つ程度の大きな破片に分かれて壊れるが、既に亀裂が入っているので同じように落とすと少しの衝撃でバラバラになって壊れるのは、経験上したことがあると思う。
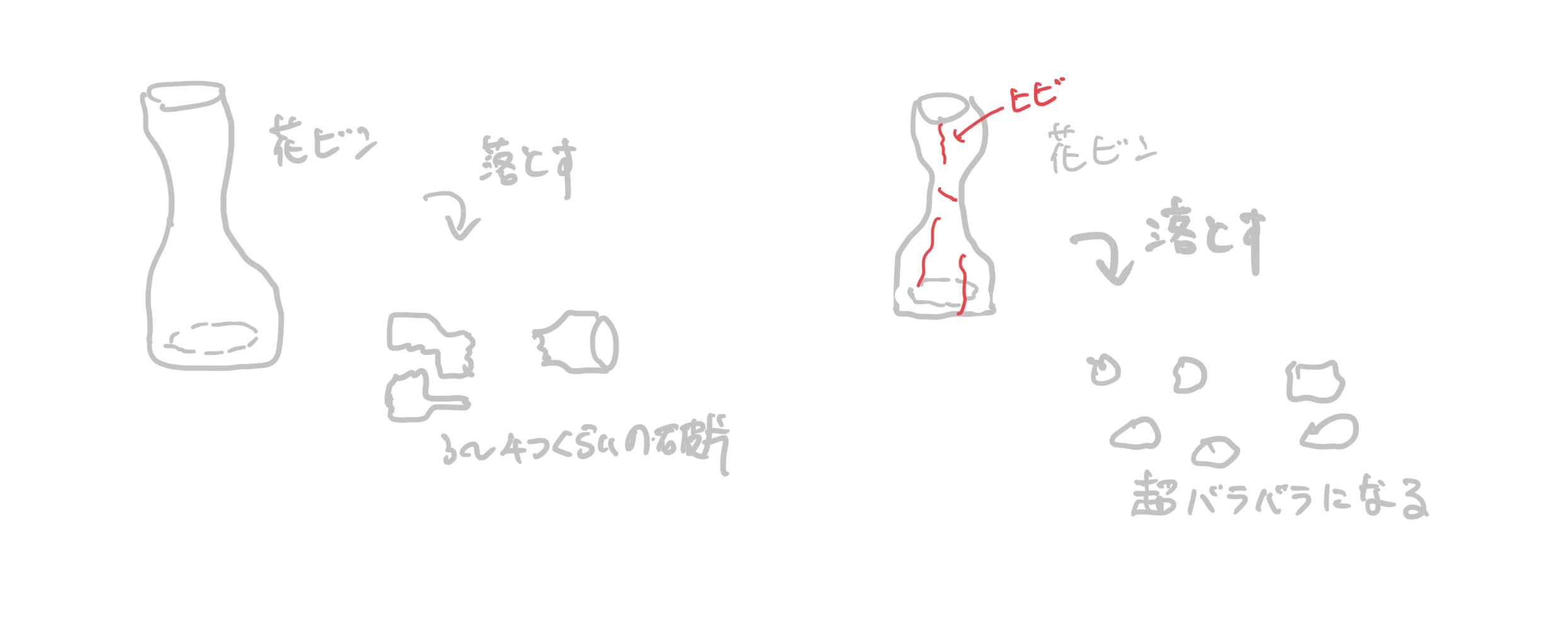
他にも例えば亀裂が入っている茶碗を亀裂に気付かずに洗っていたら、方向によっては、ちょっと触ったくらいの力で真っ二つに割れたりする。
それは金属材料も全く同じで耐久試験で壊れなくても亀裂が入っていたらかなり危険な状態で絶対にダメなのである(危ない)。
つまりこの時点で故意か、たまたまか、エンジなの能力が低いのかの原因は、特定できないが連続墜落事故に繋がる物的証拠(亀裂)は存在しており、亀裂が発見されていた可能性が非常に高いにも関わらず何故か問題なしと判断して開発を進めている(すぐ試験飛行していることより)。
これは応力集中、疲労破壊の工学の問題以前のことで試験のチェック体制、判断基準、開発システム、組織、ガバナンス、倫理に大きな問題があったとしか考えられない。
ここまでの疲労試験の問題点を挙げると
・筆者予想では疲労試験は、規模や条件から想像するに1ヶ月コースで毎日、チェックすれば30回、1日に3回チェックでも90回ほど確認できたのに亀裂を見逃した、又は無視した。
・試験が終わった部品の亀裂チェックを実施しなかった、実施したが亀裂を見逃した、亀裂に気づいたが壊れてないので無視した。
・試験を終了した時に与圧室は、破損していないので良しとした。亀裂に関しては進展していないので良しとした。
もし本当にコメットの開発現場でこんなことが起きていたらもう技術の問題ではなくモラルの問題にも繋がってくる(筆者の経験だと現場の真面目なテスト者や設計者は、亀裂の発生とその危険性について説いたが、日程に追われたり経営の責任がある課長クラスが揉み消した可能性が非常に高い)。
ここまでの構想、設計の問題を考えてきたが今回の問題がもたらした結果は、墜落事故が発生することがここで約束されたようなモノでクリティカルな問題になる。
この疲労試験の内容の杜撰さは、現代の私たちにも大きな教訓を与えてくれると思う。
次回にようやく試験飛行の内容を考えていこう。
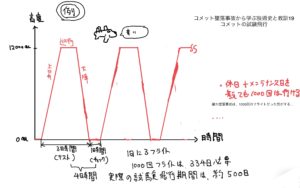
ここでオススメしたいのがアマゾン キンドル アンリミテッドだ。アンリミテッドだと数多の本が月会費だけで読める(漫画〜専門書まで幅が広い)。
今回の記事で紹介したコメットの話が紹介されている名著、失敗100選などの本が安く読める。
しかも流石、本屋が原点であるAmazonだけあって機械工学の専門書がそこそこ揃っていてかなり使えるサービスだ。
特に機械工学の専門書は高額になることが多いので少しだけ読みたい分野の本を眺めるのに非常に役に立つので是非、オススメしたい。
折角なのでさらに機械設計で必須の本があるので紹介しよう。
はっきり言って中身は不親切極まりないのだがちょっと忘れた時に辞書みたいに使える。このブログを見てくれれば内容が理解できるようになって使いこなせるはずだ。
またよく使う規格が載っているので重宝する。JISで定められて機械材料の特性が載っている。
多くの人が持っていると思うが持っていない人はちょっとお高いが是非、手に入れて欲しい。但し新品は高いので中古で購入を考えている方は表面荒さの項目が新JIS対応になっているのを確認することを強くオススメする。
また本ブログをキッカケとしてエンジニアとしてステップアップして大きな仕事を掴む手段の一つとして転職するのも一つの手だ。
やはり予算の大きい機械設計、規模が大きい機械設計、大きな仕事をする場合は日本においては大手に入って仕事をする方がチャンスの機会が多いと思う。
私も最終的に転職はしていないが自分の将来を模索していた時期に転職活動をしていくつか内定を頂いたことがある。
折角なのでその経験(機械設計者の転職活動)を共有できるように記事に起こしたので参考にして頂ければ幸いだ。
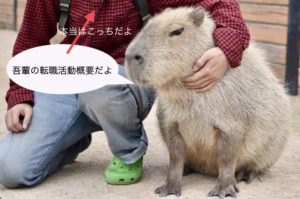
コメント